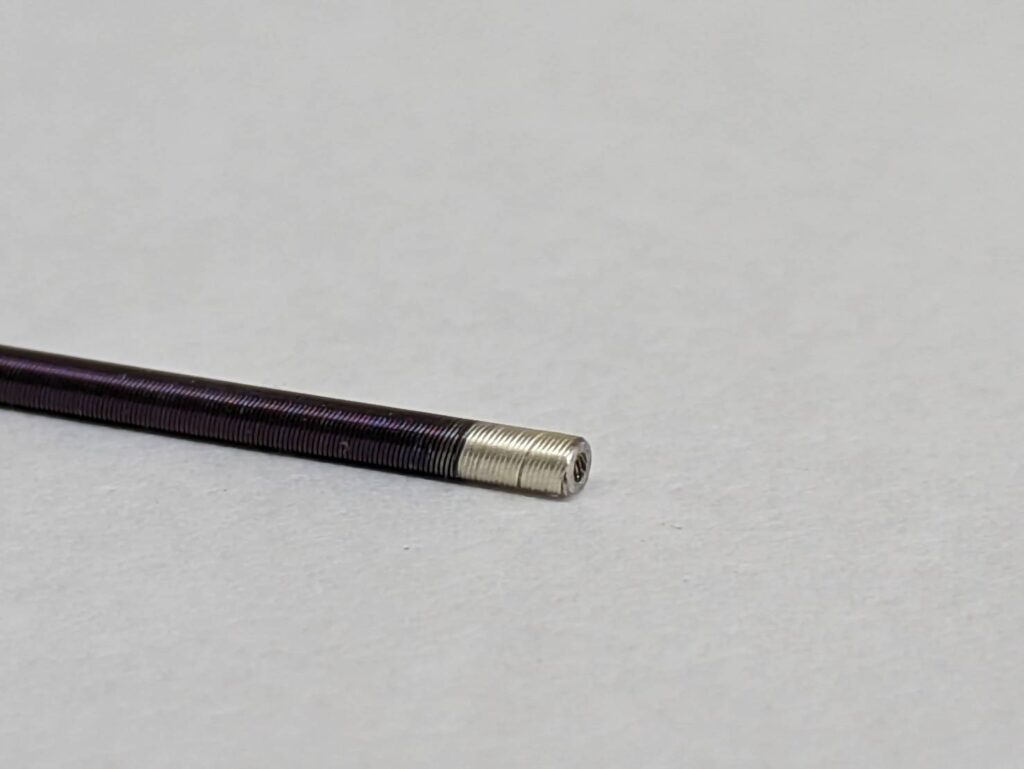
Are you satisfied with current medical wire materials for medical devices such as catheters and guidewires? Are you thinking about using new wire materials? It is quite complex to evaluate wire materials. As metal supply chain expert, we summarized key elements to evaluate wire materials. We decompose wire material selection by “design” and “supply chain”. This article equips you to make informed choices when selecting materials for medical wires. With the knowledge gained here, you’ll be able to confidently navigate the selection process.
There are 4 aspects to consider for right design of Medical Wires : Wire Type Selection, Material Selection, Geometry Design, Surface Finish / Coating. Every aspect of the medical wire needs consideration to perfectly match the application’s specific demands.
Based on the final products’ expected property, you will select wire types. For instance, a guidewire needs (high tensile) strength leading you to select strong wire types. There are roughly 6 properties and associated wire types for your reference.
Property | Wire Types |
---|---|
Straightness | Straighten Wire |
Strength | Braided Wire Wire Rope / Stranded Wire Torque Rope |
Flexibility | Braided Wire Micro Catheter |
Torquability (Torque Transmission) | Torque Wire Wire Rope / Stranded Wire Torque Rope Torque Coil |
Pushability (Manuability) | Micro Catheter |
Protection | Torque Coil Hypotube / Hypodermic tube |
Material selection is another aspect to consider, especially biocompatibility and performance.
From the biocompatible perspective, the material shouldn’t trigger adverse reactions in the body. Common biocompatible options include stainless steel (there are many types of stainless steels, even a common grade SUS304 / SS304 composes variations such as 304WPB, 304V, etc. Depending on manufacturing methods.) and nitinol.
However, material selection often involves trade-offs. For example, a highly biocompatible material such as Nitinol (Ni-Ti) might not be as strong. Also, for extremely small Diameter such as 0.003mm (3 μm) or less, stainless steel can break easily due to the impurities inside the steel so Tungsten is recommended.
There are multiple aspects for performance such as (straightness, strength, flexibility, torquability (torque transmission), pushability, and X-ray contrast, shape memory etc.). The biocompatibility and your target performance must be carefully considered to ensure the safety and effectiveness of the final product.
The geometry of the wire plays a significant role in determining its mechanical properties and performance characteristics. There are a some aspects to consider for Geometry designs.
- Size : Size such as Diameter of a single wire or Outer Diameter and Inner Diameter of strands of wires affects crucial performance of the cable. The size determines fluid flow rates in catheters, needle penetration depth, and compatibility with other components. For instance, a thin coronary stent requires a smaller diameter than a guidewire used to access a blocked artery. Depending on the use cases and applications, the size changes.
- Tolerance: Precise control over wire dimensions ensures consistent performance. Tight tolerances are crucial for catheters to maintain proper flow rates or for stents to accurately deploy and fit snugly within a vessel.
- Wire Shape: Shape variations beyond simple cylinders enhance functionality. For example, tapered wires enhance pushability / maneuverability inside the vessel and minimize tissue damage.
- Direction of Winding: This refers to the way multiple strands are twisted together to form a coiled wire. There are two directions; clockwise and counterclockwise. Clockwise winding is when the spring coils turn in a clockwise direction when you look at it from the top, while counterclockwise winding is when the coils turn in the opposite direction. The direction of winding impacts the wire’s properties if you combine with other winded components.
- Number of Layers: This refers to the number of individual strands used to create the coiled wire. The number of layers impacts several aspects:
-Overall Diameter: More layers increase the wire’s diameter, influencing its compatibility with other components and its ability to navigate tight spaces.
-Strength and Flexibility: Generally, more layers enhance overall strength but can also decrease flexibility. Finding the right balance is crucial.
-Porosity: The space between the coils is called porosity. A higher number of layers can decrease porosity, which might be desirable for certain stents that need to provide better radial support. However, it can also limit drug delivery if the stent is designed to elute medication. - Tip Design: The tip of wires can change the performance of the product. For example, Floppy tip wires reduce the potential for vessel injury during access.
The right finish / coating of a wire achieves the performance of its final product effectively. By carefully selecting the right surface finish, medical device manufacturers can optimize the performance and safety of their products.
- Oil Coating: This thin layer of oil serves a few purposes. One purpose is friction reduction. During manufacturing and manipulation, a light oil coating minimizes friction between the wire and other components, preventing wear and tear. Another purpose is corrosion protection. Oil can provide a temporary barrier against moisture and corrosion, especially during storage or transport. However, it’s important to note that oil coatings are often removed prior to final device assembly or implantation to ensure biocompatibility and proper functioning.
- Burr / Edge Treatment: After processes like cutting or machining, medical wires can develop tiny burrs or rough edges. These imperfections can snag tissue or damage catheters during insertion. Burr removal ensures a smooth, snag-free surface.
- Hydrophilic Coating: Hydrophilic coating causes water on a wire’s surface to spread out into a thin film rather than forming droplets. It prevents dirt from sticking to the wire. Hydrophilic coating allows fluids to flow more easily, reducing the risk of blockages and improving efficiency. As well, for certain implants like stents, a hydrophilic coating can also minimize blood clot formation by promoting faster blood vessel lining (endothelial) cell coverage.
- Antimicrobial Coatings: Antimicrobial coatings can help fight bacteria growth on the wire’s surface, reducing the risk of infections.
- Drug-Eluting Coatings: Certain stents can be coated with medications that slowly release into the body at the implant site.
- Electrical Conductive Coating: Certain medical devices require wires to transmit electrical signals. For these applications, a thin layer of conductive material like gold or platinum is applied to the wire surface. This coating ensures efficient transmission of electrical currents without compromising the wire’s other properties. Conductive coatings are essential for wires used in pacemakers, defibrillators, or other electrophysiological devices.
Below are some examples by use cases.
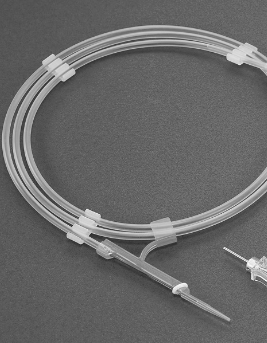
Catheter
Strength & Flexibility
>Stainless Braided Wire
Precision
>Tungsten Wire
X-ray contrast
>Tungsten Wire + Gold plating
Torquability
>Torque Wire
>Wire Rope / Stranded Wire
>Torque Rope
>Torque Coil
Protection of other components
>Torque Coil
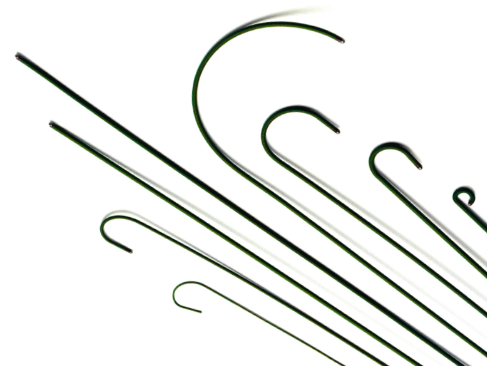
Guide Wire
Strength & Flexibility
>Braided Wire
Precision
>Straighten Wire
Biocompatibility &
Shape Memory
> Nitinol Wire
Pushability & Flexibility
>Micro Catheter
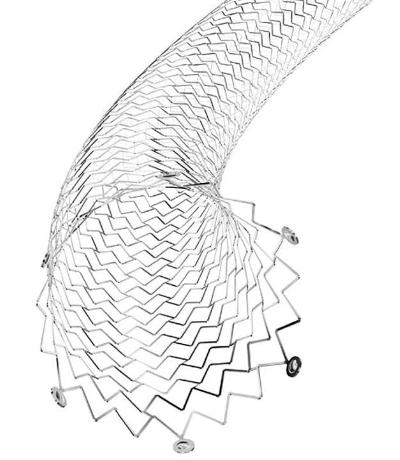
Stent
Biocompatibility &
Shape Memory
>Nitinol Wire
Strength & Flexibility
>Stainless Braided Wire
Precision
>Tungsten Wire
X-ray contrast
>Tungsten Wire + Gold plating
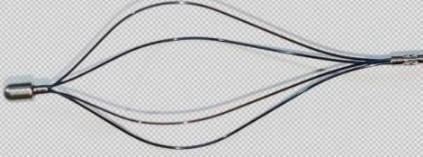
Stone Basket
Biocompatibility &
Shape Memory
>Nitinol Wire
Strength & Flexibility
>Stainless Braided Wire
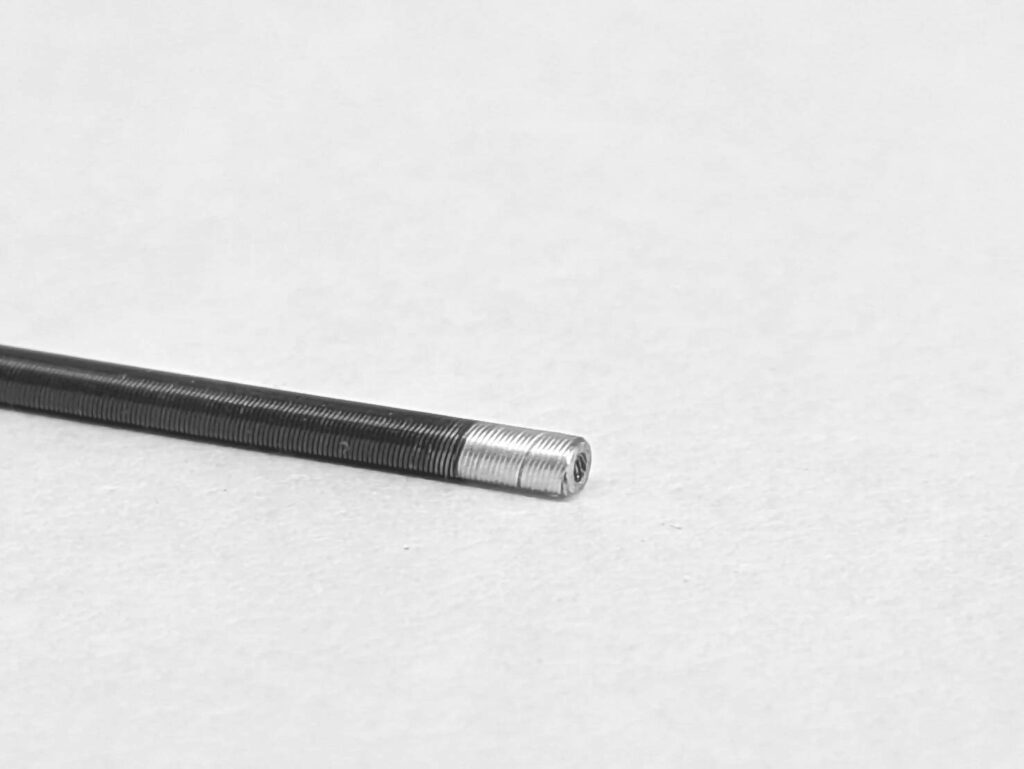
Imaging Device
Precision & Flexibility & Torqueability
>Torque Coil
Protection & Electrical Conductivity
>Hypotube / Hypodermic tube
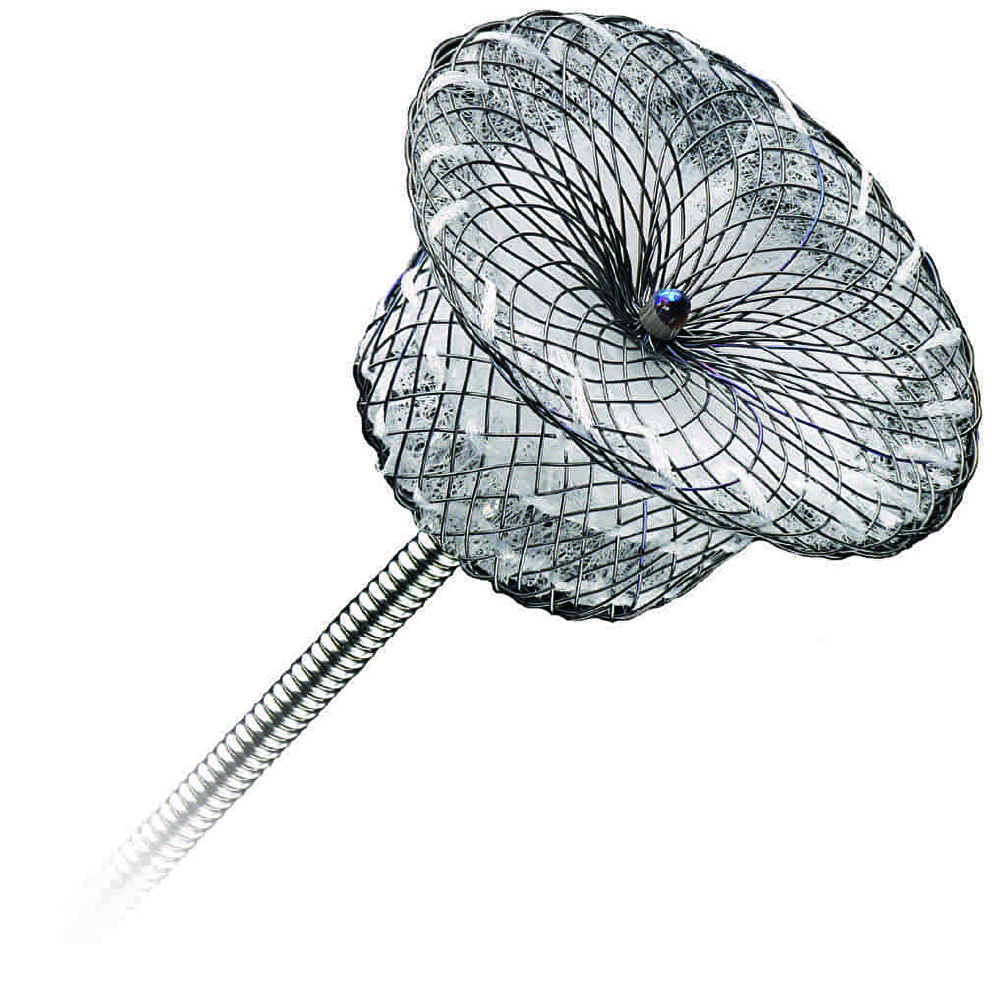
Occluder
Biocompatibility &
Shape Memory
>Nitinol Wire
There are 4 aspects to consider for right manufacturing of Wire Materials : Quality, Cost, Delivery, and Certificates. These aspects are to perfectly match the application’s specific needs.
Ensuring quality of your wire material is the first step to materialize your selection. It is a good idea to check or review your raw material choice with your specific concern (extremely thin and breakage is a critical concern etc.). There are 3 aspects about quality.
- Base Material: Even for the same steel grade, the quality of steel changes depending on steel mills. For example, SUS304 very thin wire diameter such as 0.002mm, the wire can be easily broken if the quality control is improper. This is because if impurities is concentrated or “too much” in certain places or the metalogical structure is unbalanced that when certain stress (such as bending or pulling) is applied, the steel cannot stand for and breaks.
- Processing: For the processing, the stable tolerance control and 4M control (Man, Method, Machine, Material) are one of key elements of quality control. The fewer the change or specialty from standard manufacturing methods, the easier for the manufacturer to maintain the quality.
- Inspection: The quality difference may come from the inspection methods difference. The inspection designed for the manufacturer might be different from your actual application and inspection.
Cost competitiveness of your material is another important aspect for commercialization. There are multiple factors even within one aspect. There are 4 aspects about cost.
- Raw Material: Some steel grades such as SUS304-V have extra processes to reduce impurities and increase quality of raw material. Depending on your final product application and delivery records, you may consider more common and standard grade such as high quality SUS304-WPB. The number of processes and availability makes large difference in raw material costs. Besides, depending on country or manufacturer, some steel grade & size is largely produced on regular basis so the cost is extremely competitive. It is worth while to search from other suppliers.
- Processing: Some processes are fully automated which results in cost competitive processing costs for large volumes. For relatively small volumes, the full automation can be disadvantageous due to high equipment cost or large amount of MOQ requirement. Also, the process cost changes depending on processing methods. For example, extrusion of bar materials requires high amount of MOQ while unit cost of the bar is low. On the other hand, centerless machining requires high unit cost while MOQ can be from 1 pc. By these approaches, you can consider “level of automation”, “MOQ” , “processing methods” to optimize the processing costs.
- Internal Manufacturing: If you have some internal processes that is costly or time consuming, outsourcing some processes can be advantageous. For example, imagine you can reduce the frequency of acceptance inspection if the shipping inspection is the same as acceptance inspection. This reduces not only quality control stress but also time and operational costs inside your manufacturing facility.
- International Trade: If you import from other country, exchange rate and import taxes are key elements to consider. There is an article how to check import taxes.
Delivery conditions make the final product production stable and flexible. There are 3 aspects about delivery.
- Stability: If your current source / supplier is only one or two even for a single wire category, it might be beneficial to increase sources. In case of natural disaster, pandemic, or war, having extra sources help you continue your business stably.
- Speed: Depending on country, some steel grades and sizes are regularly produced while others are less frequently circulated. This makes delivery fast or slow. Also, the larger the company size, the delivery Lead Time tends to be longer. If you could find an alternative from a smaller supplier, the delivery time tends to be faster and your production can be more flexible.
- Availability: Sometimes there is wire material distributor which owns your desired wire material. These distributors often offer at small MOQs (Minimum Order Quantities). These availabilities makes delivery extremely faster and flexible.
There are several aspects about certificate.
About certain ISOs such as ISO13485, some medical device manufactures require suppliers to own ISO13485. This is due to quality assurance perspective. There is a risk that without regulation, low quality medical devices circulate around inside the Western markets resulting in harm for the general public health. Meanwhile, in Japan, the wire material suppliers often do not own ISO13485 for two reasons. First, ISO13485 is required as medical devices. The manufacturers of medical devices must comply with ISO13485 standard and manages quality of components and raw materials by the manufacturers, not suppliers. Second, from cultural point of view, the Japanese society trusts or expects Japanese suppliers to care about the patients and not to ship any defect components and raw materials.
In my perspective, this trust is one of the Japanese characteristics different from Western or non-Japanese Societies. Western or non-Japanese society is based on the theory of Bad human nature. That is, there can be humans who behaves badly in society. So the rules of the society must be strict and prevent from those bad behaviors. In Japanese language, this is called “性悪説” (Seiakusetsu or bad human nature theory). Meanwhile, Japanese society is based on the theory of Good human nature. Humans have good behaviors so the rules of the society does not need to be strict. In Japanese language, this is called “性善説” (Seizensetsu or good human nature theory).
- ISO9001: An internationally recognized standard for quality management systems (QMS). It’s basically a set of requirements that helps organizations ensure they’re consistently providing high-quality products and services that meet customer expectations.
- ISO13485: An internationally recognized standard published by the International Organization for Standardization (ISO) specifically for the quality management systems (QMS) of medical devices.
- REACH: Registration, Evaluation, Authorization and Restriction of Chemicals. It’s a regulation established by the European Union (EU) with the primary goal of protecting human health and the environment from the risks posed by chemicals.
- RoHS: Restriction of Hazardous Substances. It’s a European Union (EU) directive that restricts the use of certain hazardous materials in electrical and electronic equipment (EEE) placed on the market in the EU.
- Test Mill Certificate: A document issued by a manufacturer to verify the quality of a material they’ve produced. It’s essentially a report about the material. It typically includes information such as chemical composition, size and tolerance, mechanical properties (tensile strength etc.) and lot number. Test mill certificate is also known as a mill certificate (millcert) or material test certificate.
Enserve offers the following support for your wire materials. If there is anything we can do to help you, we would be happy to discuss it with you.