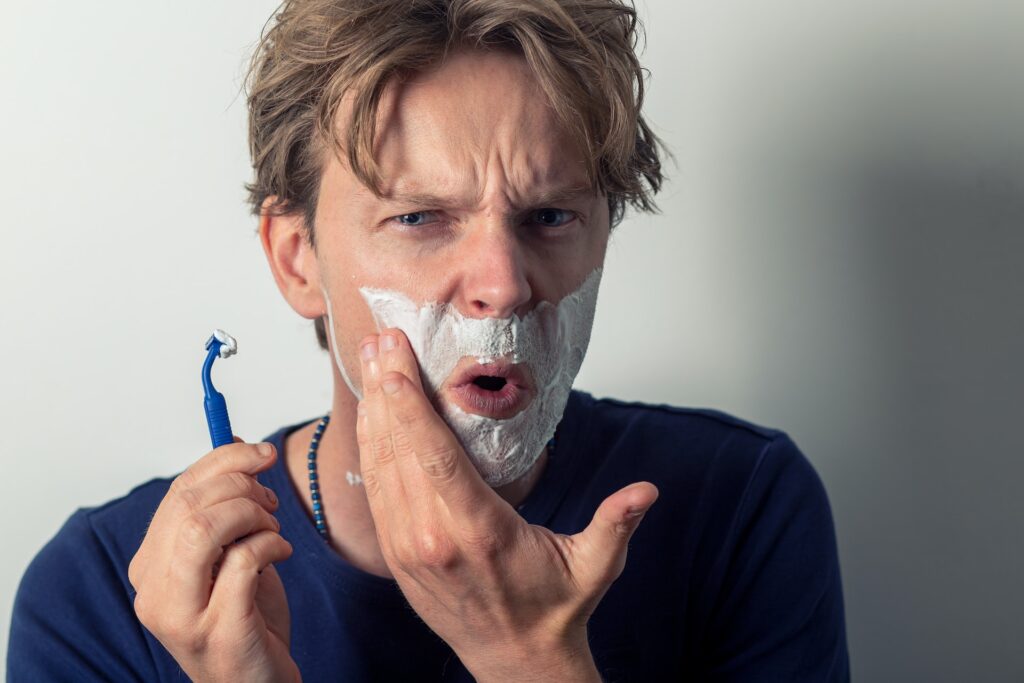
For any blades from kitchen knives to mowers’ blades and industrial blades, do you have a problem about your stainless steel blade such as dullness, rusts? It is disappointing when stainless steel (meaning it does not rust) but it rusts. It is also stressful if your blade does not perform as you wish. Besides, dull blades are dangerous because extra force to cut may cause accidents. Regrettably, stainless blades, no matter how expensive, eventually become dull or rusted as you use. In this article, the author, who has 13 years of experience in procuring metal parts and materials for Toyota Motor Corporation and startup companies, will introduce the following with my experiences. we focus on blade stainless steels (martensitic stainless steels which contain high amount of carbon and become hard after heat treatment) and present the mechanism of cutting, the reasons to cause problems, the raw material effect on cutting performance, and the possible solutions for your individual problems.
Cutting is the process of separating one material into two or more pieces by using a sharp tool or instrument. The key to successful cutting is to apply force to the material and to overcomes the material’s resistance, resulting in a split or separation. This cutting process can be broken down to 4 elements; Edge Sharpness, Material Hardness, Force, and Safety.
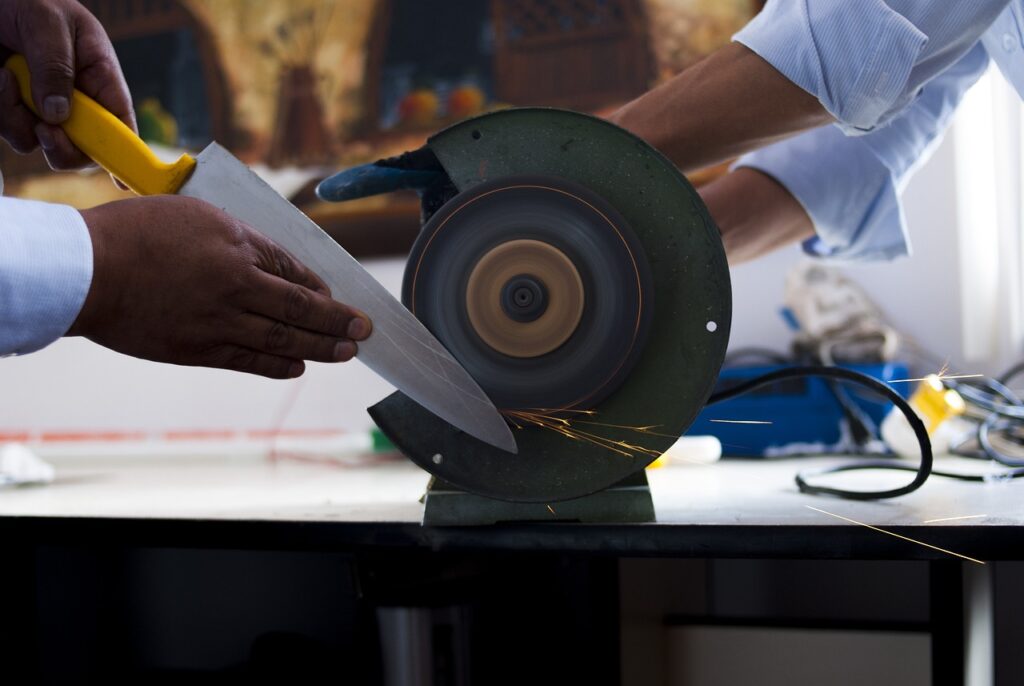
Edge Sharpness
When you apply force to a sharp edge (sharp means that The angles towards the tip of the blade are properly set and the actual tip of the blade is at an acute angle), it concentrates that force on a very small area of the material being cut. This means that you can control easily your image of cutting process and the actual cutting process. A sharp edge cleanly separates the material without causing excessive damage or deformation. It slices through the material with minimal friction or resistance, leaving a smooth and neat cut. For food example, the sharper the angle of the tip of the blade, the less damage is done to the tissue of an ingredient, so the original flavor of the ingredient is not lost and delicious food can be prepared. The sharp blades are more efficient because they require less effort to achieve the desired cut. This is especially important when cutting through tough or dense materials like wood, plastic, or metal.
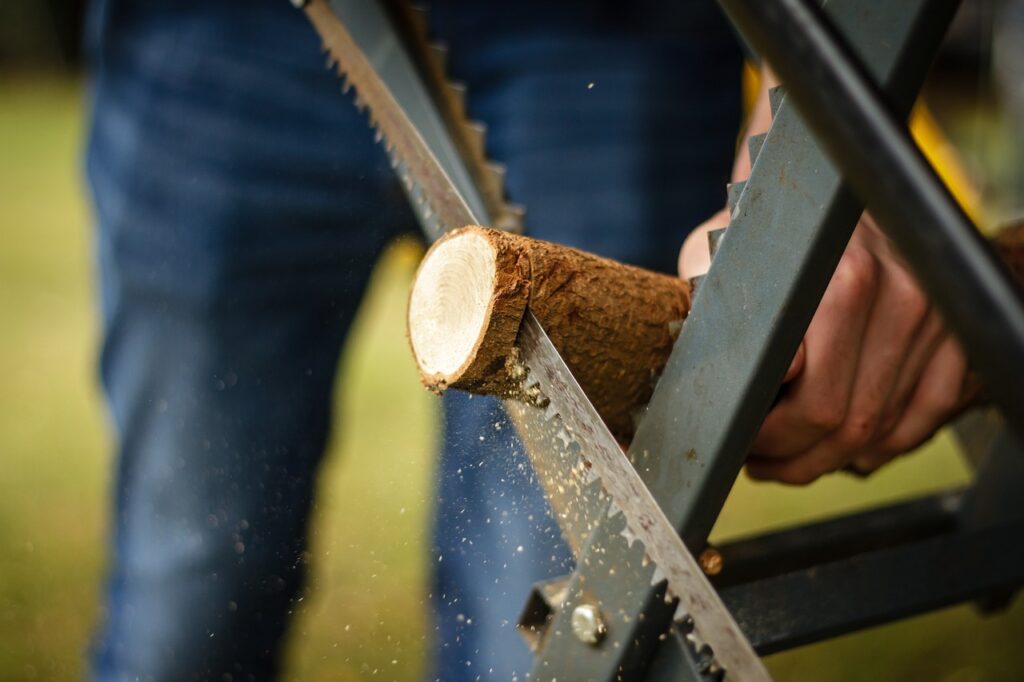
Material Hardness
The hardness of the blade material plays a significant role in the cutting process. Generally the harder the material, the higher blade cutting capability. Besides the edge, the thickness of blade material plays a role of cut consistency as well. A hard, strong blade does not bend or deform during cutting, even if it is thin, and a stable cut surface can be produced with high precision.
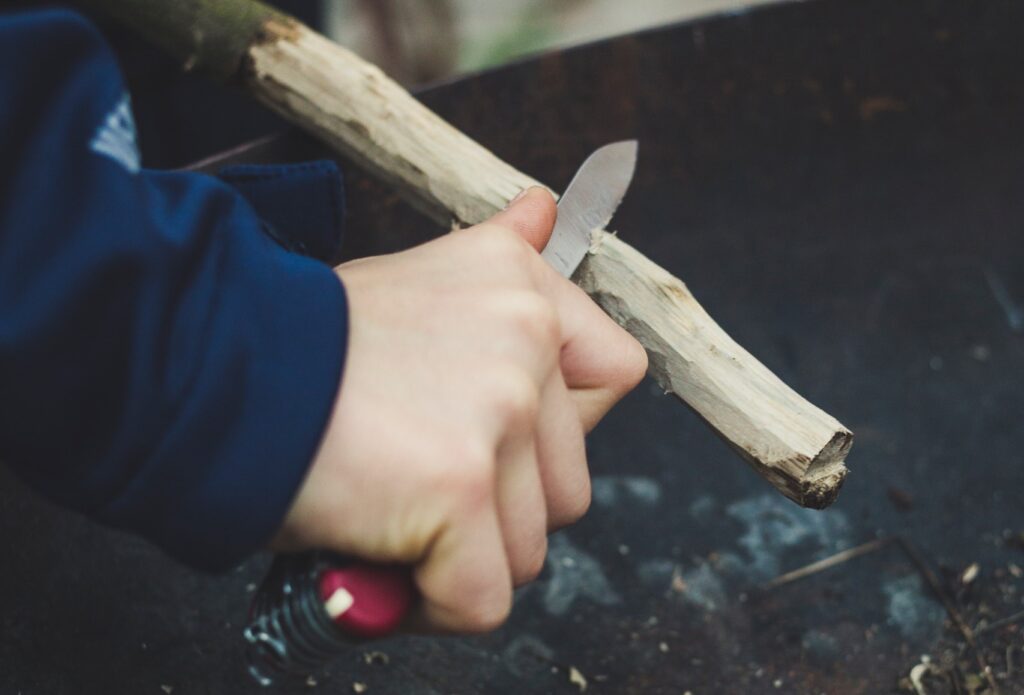
Force
To cut the material, you apply force to the blade. This force is usually in the form of pushing, pulling, or pressing down on the blade. The force is directed towards the material you want to cut. Humans can control the force while machines (particularly motors) apply the constant force so that regular maintenance of blades are essential and problematic (We have also heard of cases where machines are frequently stopped to change blades every two to three hours).
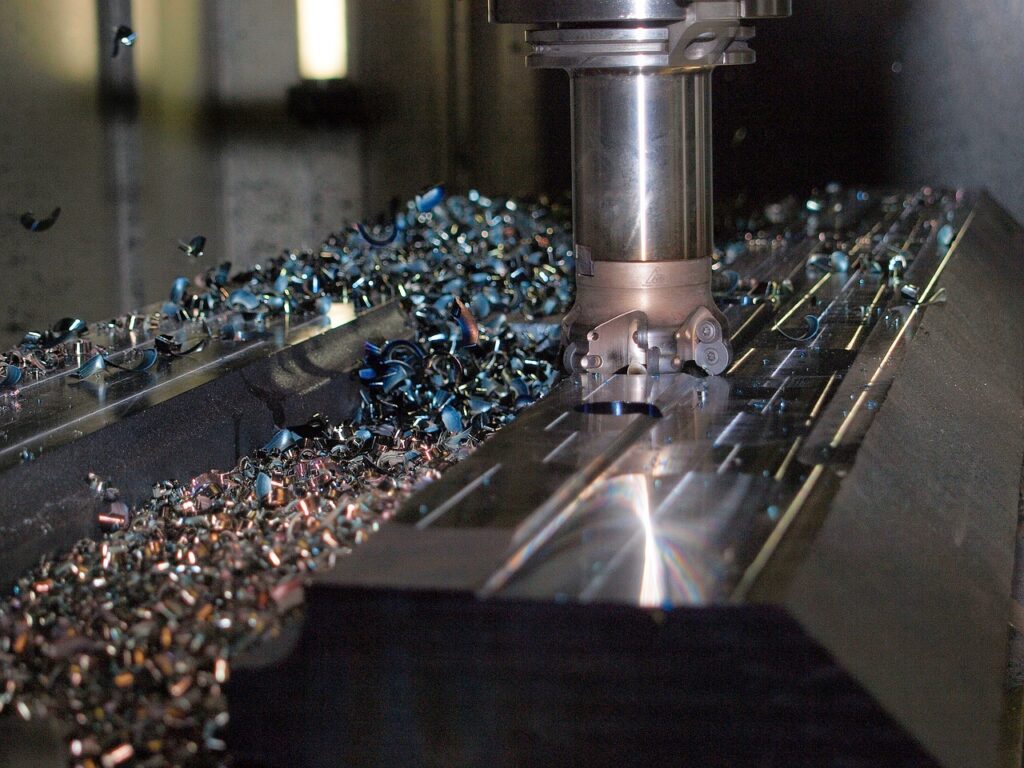
Safety
Safety is not a direct element of cutting performance, but we would like to kindly remind everyone to keep in mind about the safety of cutting process to prevent any accidents (unexpected blade injuries, fragments flying, waste slipping), health risks (exposure to dust, fumes, or hazardous substances), fires (friction heat), and contaminations (rust mixing with the food etc.).
Over time, as you use your blade, the above 4 elements change and cause problems. Most of your problems come from the 4 reasons; Edge Wear, Corrosion, Deforms or Chipping, and Heat.
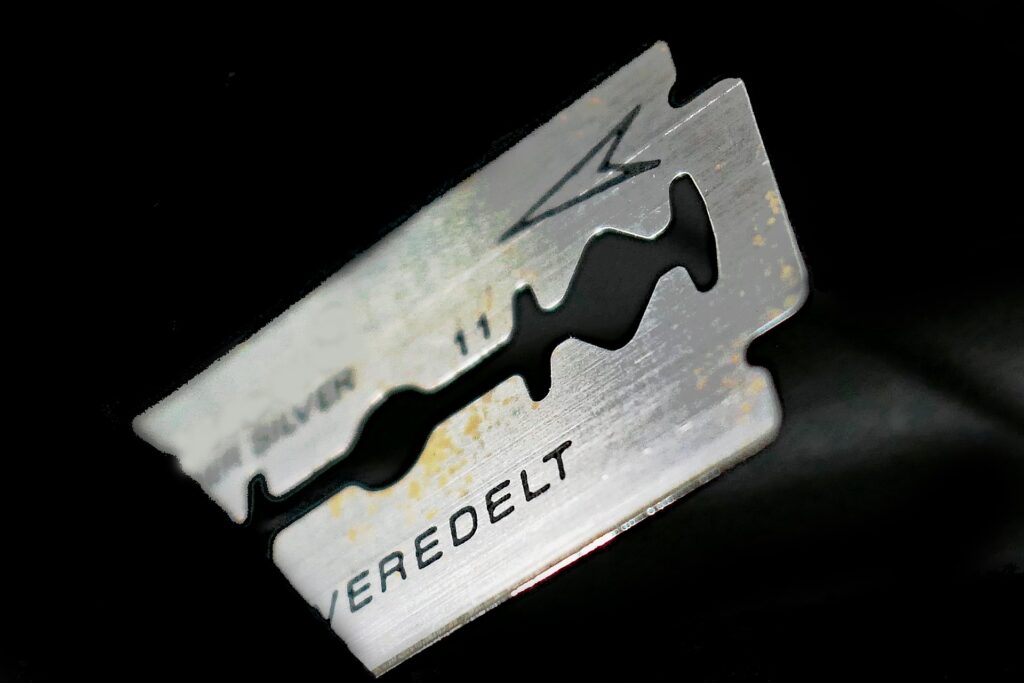
Edge Wear
Every blade is sharp at the beginning. After stroking or pressing, the edge becomes dull (lose sharpness) because every cutting process causes friction the edge of your blade. The friction causes the sharp edge to become more round. The ability of long an edge is kept sharp is called edge retention. Edge retention depends on the blade material or special coatings done on the edge (for example, razor blade has metal coating to reduce edge wear and cover chippings on edge, even though the hardness of the edge is sacrificed).
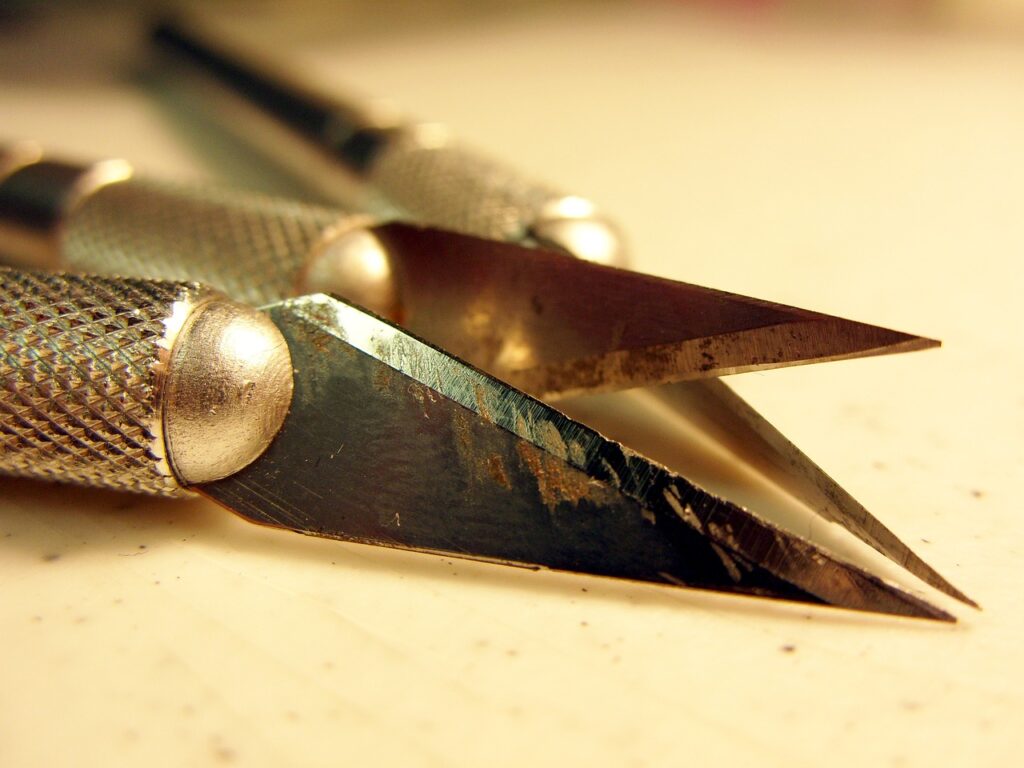
Corrosion
Even stainless steels are corrosion resistant, they corrode. Corrosion takes place with catalysts such as oxygen, hydrogen, an electrical current, dirt and bacteria (details for your reference here). Unknown to most people, blade stainless steels contain high amount of carbon which causes the corrosion more easily. A corroded blade loses the sharpness and also is no longer usable for food because the ingredients will be contaminated.
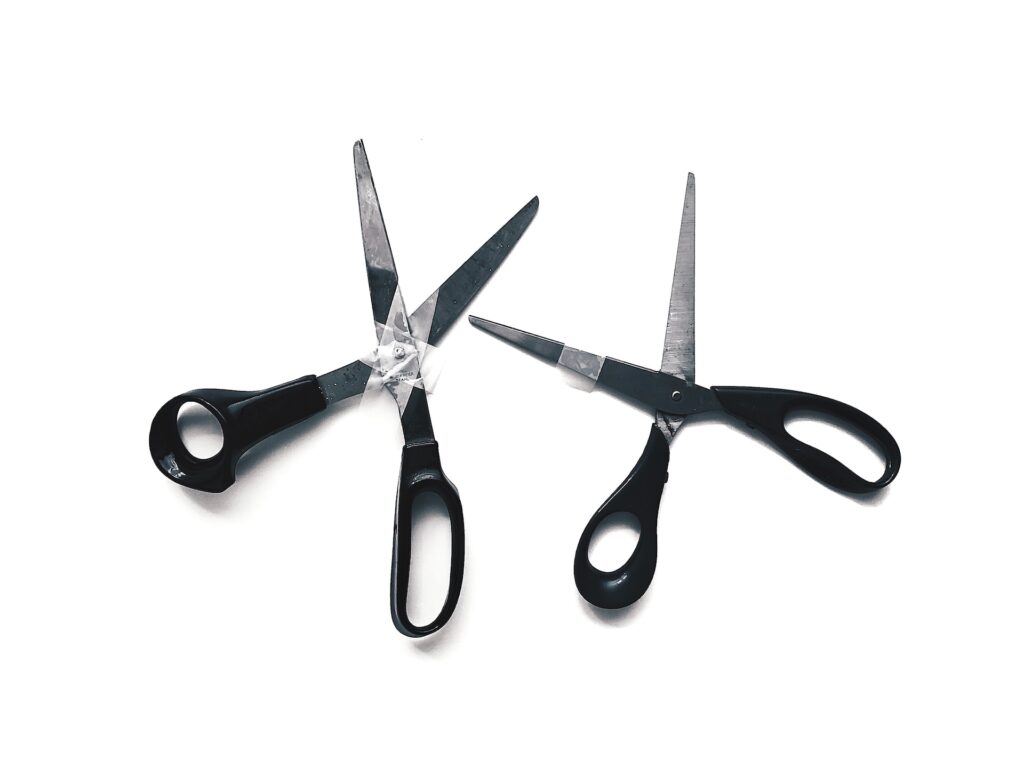
Deforms or Chipping
When blades cut too hard materials or long time, the blades may deform or chipping may occur. Deform takes place due to the direction of the force and actual cutting line do not match. Chipping takes place since carbide (tiny particle of carbon) inside the stainless steels is removed during repeated cutting motions. If blades are deformed or chipped, the blade edge is not consistent. This leads that the friction increases during the cutting process so that you need to apply greater force to cut. This is the same effect as loosing the sharpness. Also, this damages the cutting surface to cause nicks and cuts on skin (by razor blades) or bumpy cut surface (damaging the tissues of ingredients) on food.
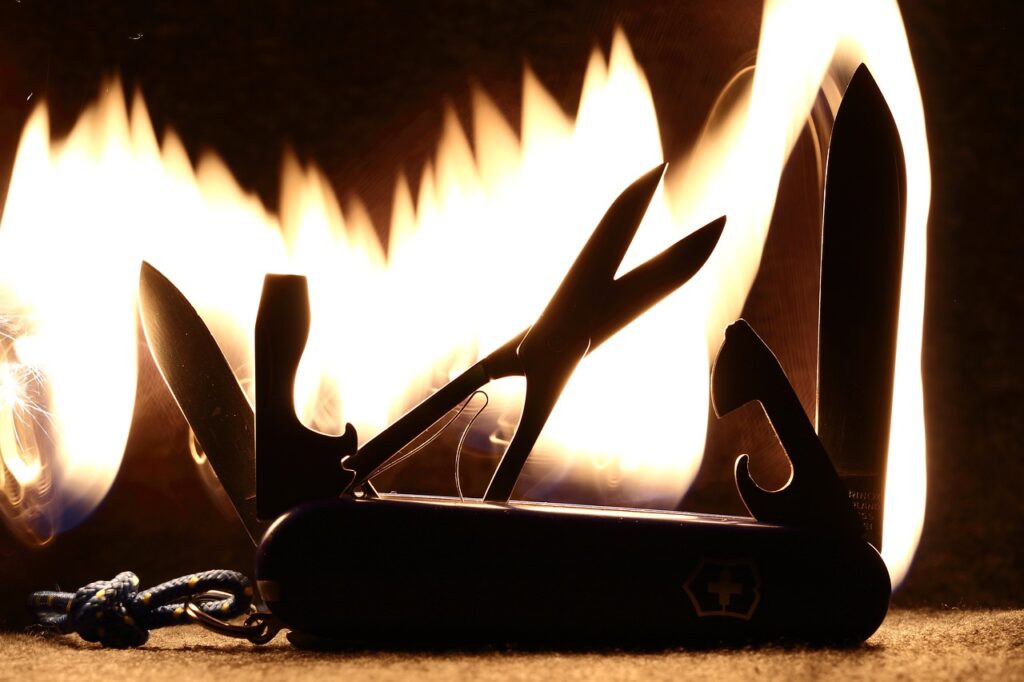
Heat
If the blade contains heats more than 100℃ or 212℉, the tempering (heat treatment to decrease the material hardness and increase the material toughness) effect starts. If the temperature reaches to 200℃ or 392℉, usually the blade stainless steels lose the material hardness and cutting ability rapidly.
From the raw material point of view, stainless steels play an important role of cutting elements for two aspects, chemical composition and raw material manufacturing processing.
If there is a stainless steel free of any changes of the cutting elements, the blade can keep the excellent performance. Unfortunately, we basically need to take a balance between the hardness and wear and corrosion resistance. This is due to the amount of carbon inside the stainless steel. If a stainless steel contains more carbon, hardness (cutting ability) increases, but it becomes more vulnerable for corrosion. Among chemical compositions, the carbon is the most important element for the blade performance.
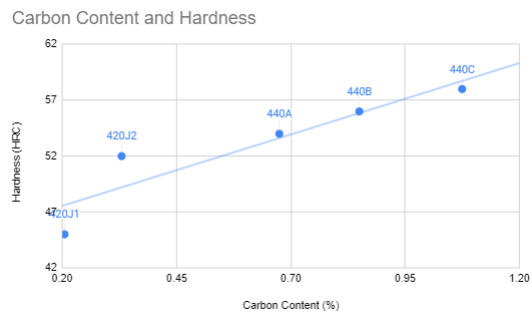
Among conventional blade stainless steels such as SUS420J2 (X30Cr13 or 1.4028), 440A (X68Cr17 or 1.4109) or X65Cr13 & X68Cr13 (1.4037). The hardness and carbon content has positive correlation. At the same time, higher carbon content makes the stainless steels easier to corrode, and becomes hard and brittle like glass, making it more prone to chipping and other problems.
Mixing carbons, chromium, and other chemicals to form stainless steel is not enough for fine blade material. To maximize the hardness after heat treatment or avoid any deforms / chipping, the manufacturing process of steel mill is also important.
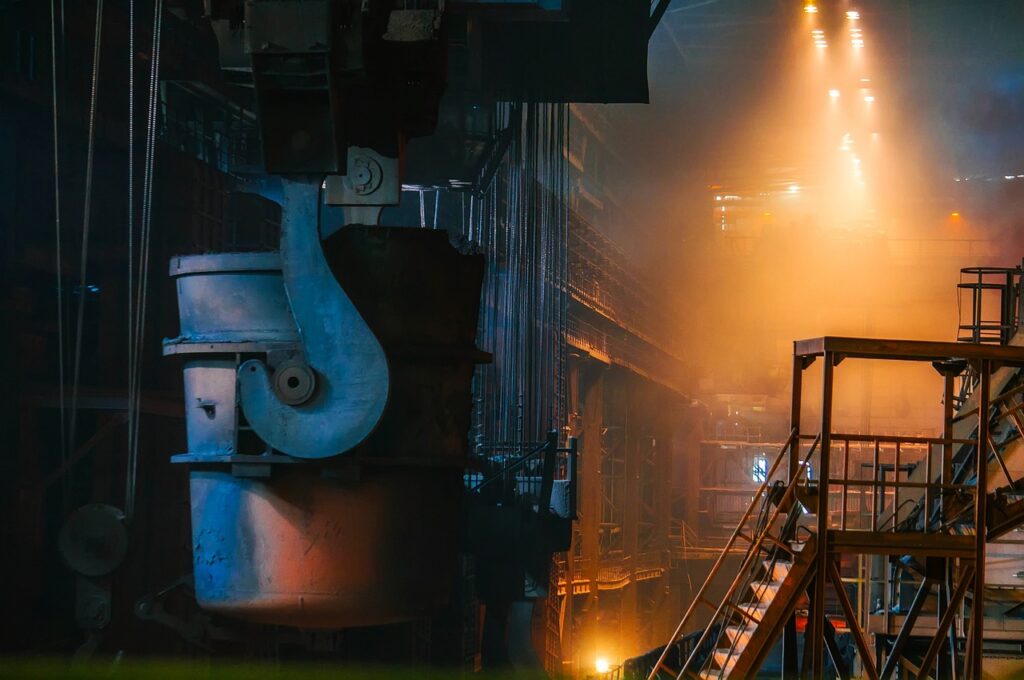
In general, to make good blade stainless steels, there are several elements to achieve high performance and quality such as impurity control (reduce unnecessary compositions or avoid their concentration), carbide size and distribution (make the particle of carbon small enough and well spread across the stainless steel), and precision control (if the material is evenly flat or straight, it will be easier for blade manufacturers to process). These are exactly the know-how of steel mills. Nippon Steel prohibits any photo or video shooting inside its plant to keep their production know-how in secret (reference).
To solve your problems about the blade from the raw material, we present the below table for your reference to reconsider material choice.
Problem | Possible Solution |
---|---|
Even sharpened blades do not cut well | More hardenable material (higher amount of carbon (C)) |
Blades are difficult to sharpen | More workable material (reducing carbon (C) and adding other chemicals) |
Blade hardness after heat treatment is unstable | Better Impurity managed material (reducing or dispersing impurities) |
Blades become dull or deforms quickly | More wear resistant material (adding other chemicals) |
Blades cause damages or bumps on cut surface & Edge frequently has Chipping | Better carbide managed material (smaller and more even distribution) or Metal coating on the blade edge |
Blades become corroded quickly | More corrosion resistant material (reducing amount of carbon (C), and adding higher amount of chromium (Cr) or adding other chemicals) |
To solve above problems, maybe we can help you find a solution. Our materials CB5 and CB6 from Japan performs exceptional hardness, wear and corrosion resistance with fine carbides. In fact, many blade manufactures do not have, or do not know options other than conventional SUS420J2 (X30Cr13 or 1.4028) and 440A (X68Cr17 or 1.4109) etc. This is not only in Japan, but also other countries as well. If you are looking for a solution to a real user’s blade problem, we may be able to help (see the product page here, but we can also find out what isn’t there).
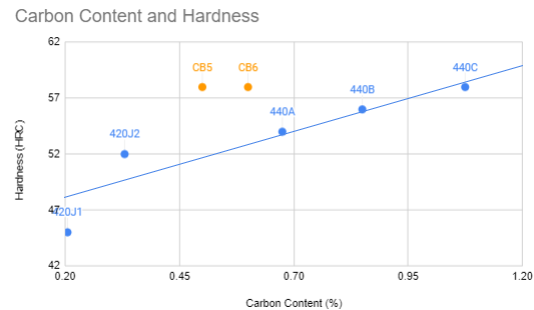
CB5 and CB6, new steel grades invented for blade manufactures perform exceptional hardness for carbon content amount. It has high wear and corrosion resistance against water, dust, and chemicals.
As we have deep understanding and knowhow of martensitic stainless steel for blade applications, sometime we offer different from customers’ specified steel grades because we wish to optimize the balance between hardness (cutting ability) and durability (against wear, corrosion such as rust). Enserve is positioned to offer unique stainless steel such as CB5 and CB6 in your required specification (coil, plate, stamped, at annealed or quenched & tempered). CB6 is ready to offer samples and commercialization in relatively short period of time. We are confident about what we offer and proud of flexibilities for small MOQs.