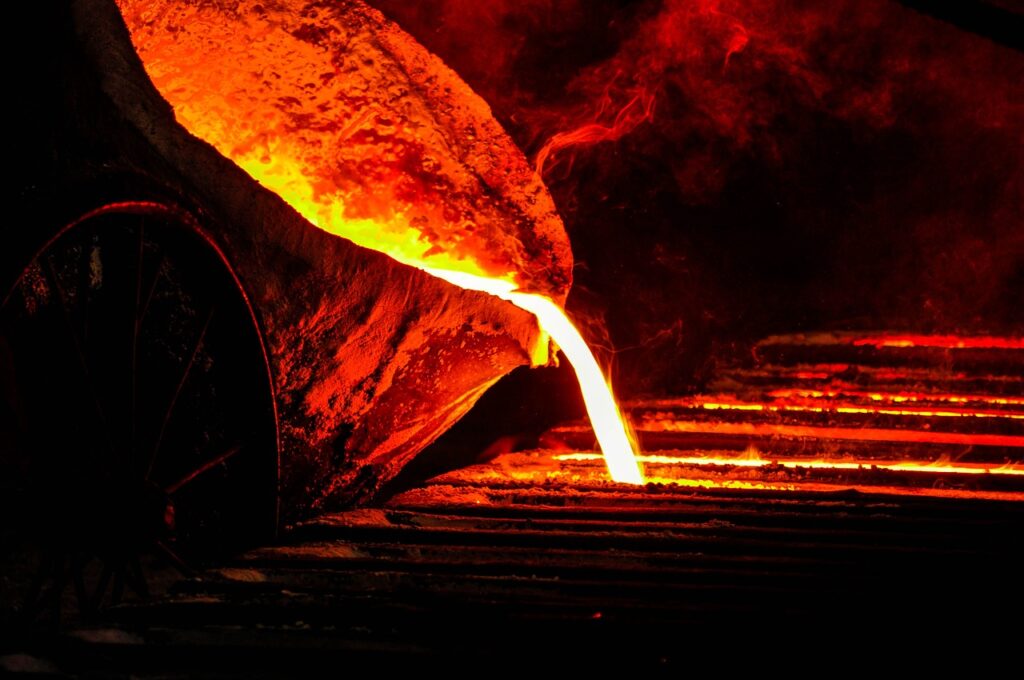
The word “steel” or “iron” or has many meanings.
In school chemistry classes, iron is the element Fe with atomic number 26, and in everyday life, people probably refer to the metal used in spoons and car bodies as steel or iron. Some people also refer to iron as the iron ore buried in the vast brown earth of Australia.
Spoons, car bodies, and iron ore are all composed mainly of Fe, but each is quite different from the other.
So in this article, the author, who has 13 years of experience in procuring metal parts and materials for Toyota Motor Corporation and startup companies, will introduce the following with my experiences.we will clarify what iron is. We will explain what the iron around us is and how it is made. We will also provide some hints as to why different steel mills have different appearances, workability, and other characteristics even for the same steel grade.
The most accurate meaning of the word iron is Fe. This element has the property of being heavy and abundant.
First of all, in terms of weight, Fe has a specific gravity of 7.86. Specific gravity is the mass (in grams) of one cubic centimeter, also called density. Specific gravity 1 is water. Therefore, Fe is 7.86 times heavier than water of the same size.
The specific gravity of gold (Au), which is considered a heavy metal, is 19.32, and that of aluminum (Al), which is considered a light metal, is 2.68, so Fe is on the heavier side.
Next, in terms of abundance, Fe accounts for 5.0% of all elements on earth, which is the fourth most abundant. The most abundant element is oxygen (O) at 46.6%, silicon (Si) at 27.7%, and aluminum at 8.1%.
Although Fe is only fourth in abundance, it is relatively heavy and accounts for 30% of the Earth’s weight. The Earth is often referred to as the planet of water, but in fact it is also the planet of iron.
Fe originated from protons and neutrons that were born in the universe 13.7 billion years ago. Helium and hydrogen were formed from protons and neutrons, and various elements were created through the phenomenon of nuclear fusion. One of the various elements is Fe.
When oxygen was created on earth, oxygen and Fe combined to form iron oxide, which was deposited to form iron ore deposits.
Iron ore deposits were formed in the ocean, but 1.5 billion years ago, the seafloor rose to the surface. These are the mines that contain large amounts of iron ore, such as the vast brown lands of Australia.
Iron ore is a mineral composed of various substances including Fe. In its natural state, Fe is tightly bound to various substances other than oxygen. Iron products cannot be made directly from iron ore. Therefore, the first step in the iron making process is to remove substances other than Fe from the iron ore.
“Iron as a product,” which is used for spoons, car bodies, etc., cannot be made directly from iron ore, nor can it be made from pure Fe extracted from iron ore alone. What is needed is coal and limestone.
In a nutshell, the reason for adding coal is to efficiently extract Fe from iron ore and limestone is to remove impurities. We will introduce them in detail in the chapter “Making Iron as a Product” in the latter part of this article.
Japan procures limestone domestically, but imports all iron ore and coal. Japan procures iron ore from Australia, Brazil, South Africa, etc., and coal from Australia, Indonesia, Canada, etc.
Globally, iron ore, coal, and limestone are obtained from the following countries
Iron ore: Australia, Brazil, South Africa, the United States, China, etc.
Coal: Australia, Indonesia, Canada, the United States, Russia, etc.
Limestone: China, the U.S., India, etc.
Iron as a product is made from raw materials such as iron ore, coal, and limestone, and there are various types of “iron as a product”.
The iron used by manufacturers is called “steel” and is referred to here as “iron as a product”.
“Iron ore + coal + limestone” are processed as the following to make “iron as a product”.
●Iron ore + coal + limestone
↓
● Pre-processing
↓
●Making steel in a blast furnace
↓
● Make pig iron in blast furnace
↓
● Turned into billets
↓
● Turned into billets (= “iron as a product”)
This process requires an incredibly large facility called a blast furnace, which only three companies in Japan have. The following is an introduction to the process of making steel as a product.
Simply melting iron ore is not enough to extract Fe. Here, sintered ore and coke are produced.
Coal is steamed at 1,300°C or higher to make coke. Iron ore is then crushed, mixed with coke and limestone, and baked. This is sintered ore.
When coal is converted into coke, the calorific value increases dramatically, enabling high temperatures to be generated. Coke also makes it easier to extract Fe from iron ore. When limestone is added, impurities such as silica and alumina in the iron ore can be removed.
The largest piece of equipment used in the production of “iron as a product” is called a blast furnace, which is approximately 100 meters high and has a base area as large as a tennis court. The only companies in Japan that have blast furnaces are Nippon Steel, JFE Steel, and Kobe Steel, and these three companies are called blast furnace mills. Other steel mills own electronic arc furnaces (EAF) and are called electronic furnace mills. We will introduce briefly how electronic furnace mills make “iron as a product” at a later chapter.
In a blast furnace, iron ore, sintered ore, and coke are heated. The temperature reaches 2,000 degrees Celsius because of the coke. A sludgy substance is formed at the bottom of the blast furnace, which is called pig iron.
Pig iron is like the prototype of “iron as a product”. Blast furnaces continue to operate 24 hours a day, 365 days a year, and therefore continue to be used for years. Therefore, ore shavings continue to accumulate in the blast furnace, and newer and well-maintained furnaces seem to be more stable in terms of quality than older ones.
Blast furnaces play an important role in the decarbonization of the steel industry. Blast furnaces currently burn gas, which emits large amounts of carbon dioxide, and many countries are considering changing some of the fuel used in blast furnaces to hydrogen (which emits water instead of carbon dioxide after combustion) or using large electric furnaces.
The percentage of blast furnace production is 91% in China, 75% in Japan, 57% in Europe, and 30% in the United States. In the U.S., electric arc furnaces are the main production method historically because of their flexibility in furnace operation and easier access to scrap materials compared to blast furnaces.
Pig iron iteself is too hard and brittle for “iron as a product”. Therefore, pig iron is transferred from the blast furnace to a converter and undergoes a process called refining. This process turns pig iron into steel.
Steel has less carbon than pig iron, which makes it more durable and usable as “iron as a product”.
In this process, impurities such as silicon, phosphorus, and sulfur are removed from pig iron. When lime is added to the converter, it compounds with the impurities and forms a lump. These lumps are called slag.
In the converter, manganese, silicon, aluminum, and other elements are added to adjust the chemical composition to produce steel.
The blast furnace has a volume of 5,500 cubic meters, and blast furnace makers produce 12,000 tons of pig iron per day. From there, the steel is divided into smaller portions and made into steel in the converter, but the volume is still enormous.
Steel is the material for steel products, but it takes a lot of time and effort to process the steel made in the converter and deliver it directly to the steel manufacturer.
Therefore, blast furnace makers process the steel as it is after it is made.
The steel in its sludgy state is poured into a mold to form a shape. The equipment used in this process is called continuous casting equipment. Continuous casting equipment turns sludgy steel into semi-finished steel pieces.
There are several types of steel pieces such as billets, blooms, slabs, and ingots.
A billet is a cylindrical bar for extrusion to form wire rods, round bars, or square bars. A billet is thinner than a bloom.
A bloom is a long bar with a square cross section more than 130 mm per side. A bloom is used for rolling to form a large pieces of steel such as billets and structual steels.
A slab is a rectangular cross section plate with a thickness of 50 mm or more and a width of 300 mm or more. A slab is used for rolling to form Hot Roll Coil and Cold Roll Coil.
An ingot is shaped according to the manufacturer’s requirements. An ingot is used to form pipes and tubes.
Even a piece of steel is not yet “steel as a product. Steel products made by processing steel billets become “iron as a product.
Steel materials include wire rod, thick plate, thin plate, round steel, bar, and steel pipe.
The relationship between steel billets and steel products is as follows.
Steel Piece | Steel Product Examples |
Billet | Wire rod, Round Bar, Square Bar |
Bloom | Structual Steel, Billets |
Slab | Hot Roll Coil, Cold Roll Coil, Plates, Sheets |
Ingot | Steel Pipes and Tubes |
Three leading Japanese blast furnace makers produce steel products as follows.
Nippon Steel produces coils, plates, sheets bars, pipes, and wire rods.
JFE Steel produces coils, plates, sheets, steel pipes, steel bars, and wire rods.
Kobe Steel, Ltd. manufactures coils, plates, sheets, bars, and wire rods.
Each company often produces large quantities of steel for automotive applications. In addition, the process of processing each steel material can cause differences in external finish and internal performance, and each steel manufacturer has processing know-how and custom-made processing facilities.
End users (manufacturing companies) such as tableware manufacturers and automobile manufacturers purchase steel products that can be easily processed into the shape of their products to make spoons and automobile bodies.
The “iron as a product” introduced so far is, so to speak, the most basic type of iron. Special steels are made by adding various metals other than Fe. Both blast furnace mills and special steel mills have furnaces for manufacturing specialty steel, although the processes are slightly different.
Blast furnace mills make pig iron from minerals such as iron ore, coal, and lime, remove impurities in a converter, and then adjust the metal chemical composition (remove carbon and add necessary metal components) in a gas furnace. Other than blast furnace mills are called electric furnace mills because they use electric furnaces instead of blast furnaces. Electrodes are inserted into an electric furnace filled with scrap iron and other materials, and an arc discharge is generated on the electrodes. This generates high-temperature heat, which melts steel scrap and other metals to produce molten steel. The molten steel produced in the electric furnace is further conditioned in a gas furnace. Both blast furnace and electric furnace makers perform component adjustment in the gas furnace, which is called secondary refining. Secondary refining is an important process for manufacturing special steels because it is the final step in adjusting the concentration of the elements that determine the properties of the steel.
Even with the same steel grade, there may be no problem with Stell Mill A’s steel when it is bent or heated, but Steel Mill B’s steel may break or fail to have the expected characteristics. One of the reasons for this difference is due to the secondary refining process (removal of impurities and the use of trace amounts of metal additives that are not listed in the material properties as “secret ingredients”). For this reason, some customers specify to purchase such as “SUS304 made by Nippon Steel”.
How was this story? Iron is all around us, but iron as a product is quite different from the pure elemental symbol Fe. The raw materials are iron ore, coal, and limestone to which various metallic elements are added and processed before they can be used. The processing methods are also diverse, and are about to evolve further toward a carbon-neutral society.
We place importance on proposing steel products that meet our customers’ QCD expectations, and in some cases, we work to trace back to the manufacturing process of the steel raw materials to solve our customers’ problems.