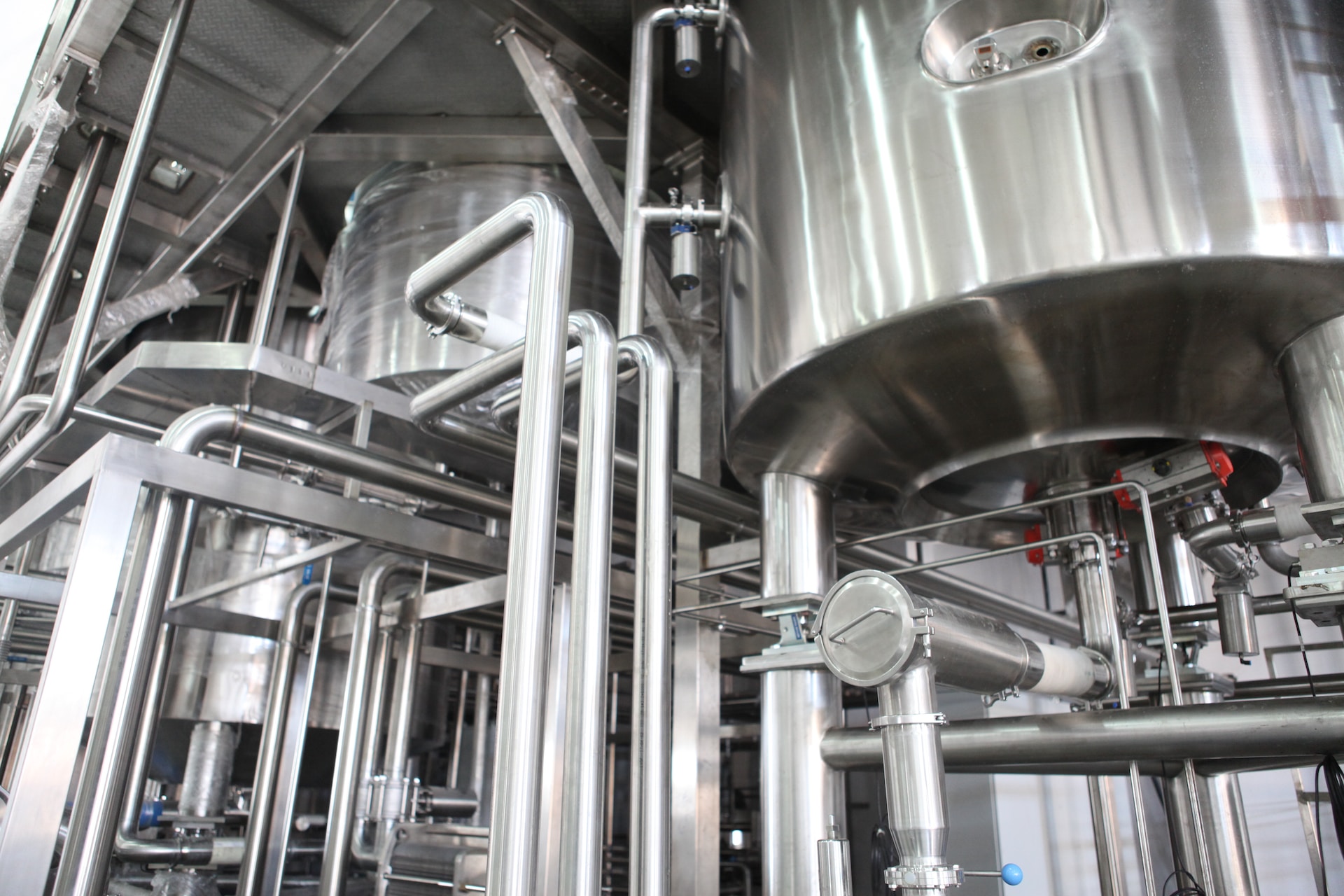
Have you heard of “304 stainless”, “18/8 stainless”, or “1.4301 stainless”? Even if you haven’t heard of these names, you must have seen this stainless steel grade in your life. It is used in everywhere from kitchenware to Aerospace components. Stainless steel 304 is the most popular and most widely used of the stainless steel family. If you would like to know about stainless in general, you can refer to our general introduction of stainless steels.
304 is known for its excellent corrosion resistance, weldability, and formability. The equivalent steel grades are AISI304 (USA) / X5CrNi18-9 1.4301 (Germany) / X5CrNi18-10 (France, Italy) / SS304. We hereby call it 304 for convenience. In this page, we introduce the properties of 304, Chemical Compositions by equivalent steel grades, dimensions and shapes available, and quality essence to avoid failures of using 304 that we care about. This is a long complete guide of 304. Please refer to the contents and jump to the section of your interest.
304 is often referred to by its old name 18/8, which is derived from the chemical composition of this stainless steel being 18% chromium and 8% nickel.
304 is an austenitic stainless steel. Austenitic stainless steels contain high amount of chromium and nickel (austenitic stainless steels are the only stainless steel that contains nickel). Austenitic stainless steels form a metallurgical structure called austenite at room temperature (nickel plays a role of making austenite crystal structure which is tough for processing and welding at room temperature, instead of 1000℃ temperature).
Stainless steels contain Chromium and form a thin, passive layer of chromium oxide (in short a film) on the surface of the metal. The chromium oxide layer prevents oxygen from reaching the underlying iron, which prevents rust from forming. Nickel stabilizes the passive film formed by chromium oxide and improves corrosion resistance. Compared with other stainless steels, Austenitic stainless steels such as 304 are highly resistant to corrosion, tough and has excellent weldability, although it cannot be heat treated.
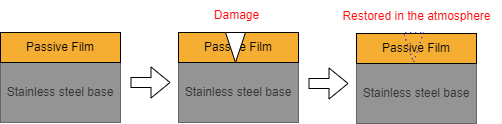
304 is relatively easy to weld, and does not require any post-weld heat treatment. This makes it a popular choice for applications where welding is required. We would like to remark kindly that 304 could be vulnerable for corrosion if it is heavily welded because welding causes high temperature of the steel making the Sensitization. Sensitization is the phenomenon whereby carbon and chromium combine when stainless steel is heated to around 550-900°C, reducing its corrosion resistance (details in Intergranular Corrosion). As a sensitization measure, there is another steel grade called X2CrNi18-9 / 1.4307 / 304L, where there is less carbon inside the steel to reduce sensitization.
SUS304 is the most widely used stainless steel grade in the world, due to its excellent corrosion resistance, weldability, and formability. It is used in a wide variety of applications, including:
- Medical devices
- Construction materials
- Automotive components
- Chemical processing equipment
- Marine hardware
- Food processing equipment
For tips, blade material expert, we know that 304 is also used for blades for mixer where the corrosion resistance has priority over continuity of sharpness (this is why your mixer gets stuck with full of food easily, it becomes dull easily).
Plus, for some applications, there are special types of 304 such as 304V. 304V is double or triple melted stainless steel. 304V is initially electric-arc melted followed by a Vacuum Arc Re-melt (VAR). This melting practice minimizes contaminants while yielding a more uniform metallurgical structure. 304V is used in severe environment such as medical wires or aerospace components.
304 is non-magnetic. This is because it has an austenitic crystal structure at room temperature. Austenitic stainless steels are non-magnetic due to the presence of nickel. Nickel distorts the crystal structure of iron, which makes it difficult for the magnetic domains to align. As a result, austenitic stainless steels are non-magnetic.
However, 304 can become slightly magnetic if it is cold worked. Cold working is a process of deforming the metal at room temperature. Cold working can cause stresses inside 304 and change in the internal crystalline structure, which can result in parts of the material having a magnetic crystalline structure. The amount of magnetism that is induced in 304 by cold working depends on the severity of the cold working process. More severe cold working will result in more magnetism.
One effective remedy for magnetism is heat treatment. By applying the appropriate heat treatment to the 304, it is possible to restore the altered crystalline structure and remove magnetism of 304. Another remedy for magnetism is using other stainless steel grade such as 304L (X2CrNi18-9 / 1.4307) or 310S (X6CrNi25-20 / 1.4951 / X8CrNi25-21 / 1.4845).
Adjusting the properties of a metal material by cold working (rolling) or heat treatment is called thermal refining. The main property that changes as a result of thermal refining is strength (tensile strength, hardness, etc.) and surface finish. 304 adopts thermal refining methods including “Tempering (for strength)” and “Bright Annealing (for surface finish)”.
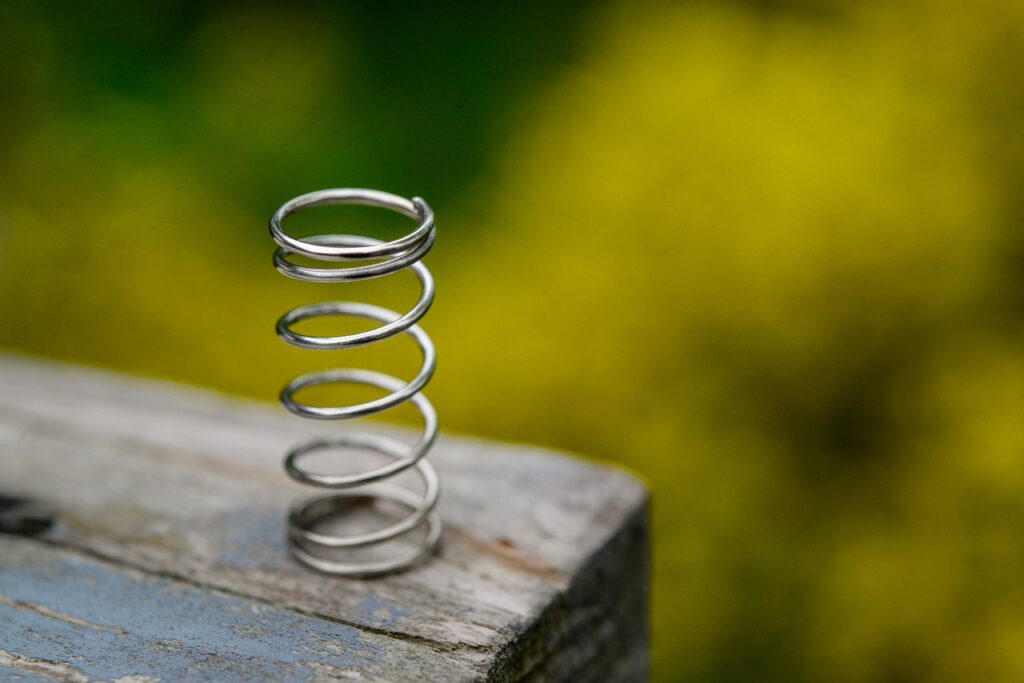
Sometimes 304 has variations such as 304-“CSP-1/2H”. These steels are tempered (heat treated) and cold rolled 304 for spring applications. “CSP” stands for “Cold-rolled Strip for SPRING” and “1/2H” indicates the level of hardness or strength of the material.
As well Tempering is conducted in the range of 250 ~ 500ºC, 30 minutes to 4 hours for wire and 250 ~ 500ºC, 30 minutes to 24 hours for strip. This tempering is to remove the stress inside steel for further processing. The reduction rate (the rate of thickness change from input thickness to output thickness) of the cold rolling process is used to distinguish the temper rate (higher rate for higher hardness).
Temper Symbol | Hardness Min HV | Yield Strength Min N/mm2 | Tensile Strength Min N/mm2 | Elongation Min % |
---|---|---|---|---|
1/2H | 250 | 470 | 780 | 3 |
3/4H | 310 | 665 | 930 | 3 |
H | 370 | 885 | 1130 | 3 |
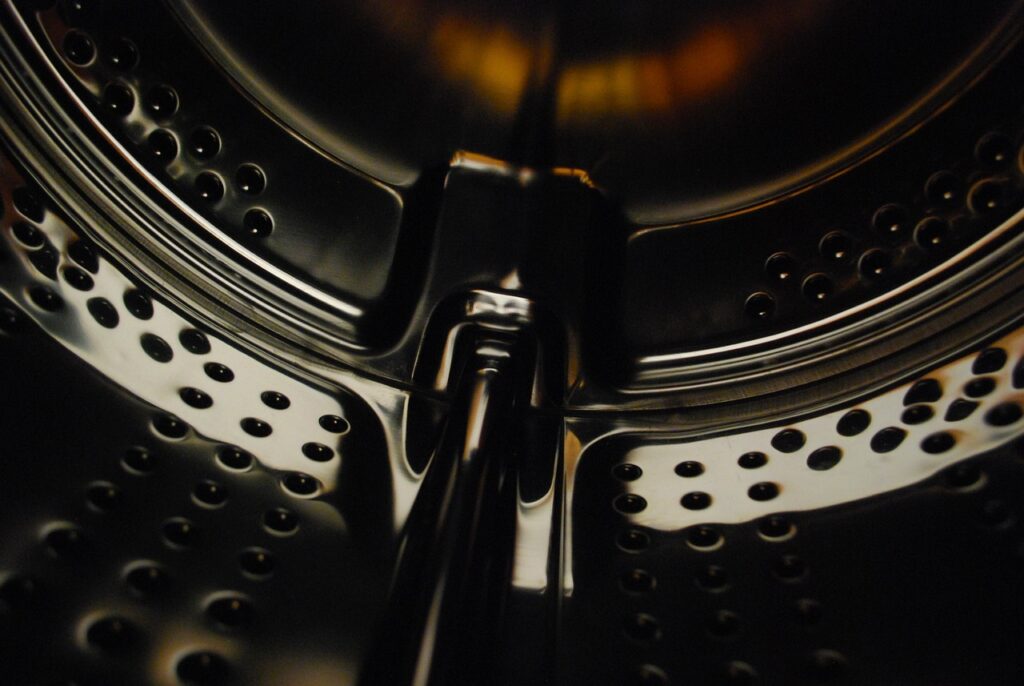
304 has variations of surface finish or appearance depending on how it is processed. One type of annealing called Bright Annealing makes the stainless smooth, reflective, and has a mirror-like appearance. Bright Annealed surface is called BA Finish. You can image BA finish from the inside steel used for cloth dryer of this picture.
Bright annealing is typically performed in a vacuum or in a controlled atmosphere (in short annealing furnace) containing inert gases, such as hydrogen or nitrogen. This prevents the metal from oxidizing during the annealing process.
The typical annealing temperatures for stainless steel range from 1000 to 1200 ºC.
304 has excellent corrosion resistance due to the passive film described above, but depending on the environment in which it is placed, this can be destroyed and corrosion can occur. The main environmental factors affecting corrosion are the type of acid and pH (a measure of acidity or alkalinity) of the solution, the amount of dissolved oxygen in the solution, the presence of halogenated elements (Fluorine (F), chlorine (Cl), bromine (Br), iodine (I), etc.), and the temperature of the environment. You can refer to the corrosion mechanisms, types, and solutions for further details.
Below table indicates a list of chemicals that corrode 304. Please be aware for the following substances and solutions because they corrode 304.
Organic Substance | Inorganic Substance | Inorganic Substance | Inorganic Substance |
---|---|---|---|
Carbon tetrachloride (containing water) | Sulfuric Acid (Above 40%) | Chlorine Gas (containing water) | Sulfurous Acid Gas (containing water) |
Trichlorethylene (containing water) | Ocean Water | Silver Salts | Calcium Chloride |
Nuonic Acid | Zinc Chloride | Aluminum Chloride | Ammonium Chloride |
– | Sulfur (molten) | Bromine | Hypochlorite |
– | Ferric Chloride | Ferrous Chloride | Hydrochloric Acid |
– | Mercury Salt | Phosphoric Acid | Chlorine Gas (dry) |
– | Potassium Chloride | Salt Water | Barium Chloride |
– | Copper Chloride | Magnesium Chloride | Sulfurous Acid Gas (dry) |
The below comparison table demonstrates the difference between 304 and other similar and often compared stainless steels (304L, 304H, TP304, 316, 301, 303, 430, SCS13) for your material selection reference. Equivalent European steel grades are also available in this table.
Steel Grade | Difference from 304 | Advantage over 304 | Disadvantage over 304 |
---|---|---|---|
304L X2CrNi18-9 1.4307 | Lower Carbon (C) content | Less sensitization | More expensive, longer LT |
304H X6CrNi18-10 1.4948 | Higher Carbon (C) content | Strength under high temperature (up to 800ºC). For 304, Strength up to about 525ºC | Easy for sensitization |
TP304 X5CrNi18-9 1.4301 | 304 for “Tube Pipes” | Suitable for 304 tubes and pipes | Not suitable for other uses |
316 X5CrNiMo17-12 1.4401 | Molybdenum (Mo) added | More corrosion resistance | More expensive |
301 X5CrNi17-7 1.4319 | Reduced Chromium (Cr) and Nickel (Ni), high Carbon (C) content | Increased strength by cold working for spring applications | Less corrosion resistance |
303 X10CrNiS18-9 1.4305 | More Phosphorus (P) and Sulfur (S) | Better machinability | Less corrosion resistance |
430 X6Cr17 1.4016 | No Nickel (Ni) | Lower price, better formability and weldability | Less corrosion resistance, magnetic |
SCS13 G-X6CrNiMo18–10 1.4308 | 304 equivalent for casting | Suitable for casting | Not suitable for other uses |
The below table indicates the chemical compositions of 304 and other stainless steels.
The Carbon (C) content in this table is low to improve its formability. High carbon content can make the steel more difficult to form and can also reduce its corrosion resistance.
The Silicon (Si) and Manganese (Mn) content improve weldability. Manganese helps to reduce hot cracking during welding. Silicon helps to remove oxygen and nitrogen from the molten pool during welding, which also reduces the risk of hot cracking.
The Nickel (Ni) and Chromium (Cr) content provide excellent corrosion resistance. Chromium forms a thin, passive layer on the surface of the steel that protects it from corrosion. Nickel helps to stabilize the passive layer and makes the steel less susceptible to pitting and crevice corrosion.
Steel Grade | C | Si | Mn | P | S | Ni | Cr | Other |
---|---|---|---|---|---|---|---|---|
304 X5CrNi18-10 1.4301 | ≦0.07 | ≦1.00 | ≦2.00 | ≦0.045 | ≦0.03 | 8.00-10.50 | 18.0-20.0 | – |
304L X2CrNi18-9 1.4307 | ≦0.03 | ≦1.00 | ≦2.00 | ≦0.045 | ≦0.03 | 8.00-10.50 | 18.0-20.0 | – |
304H X6CrNi18-10 1.4948 | 0.04-0.10 | ≦1.00 | ≦2.00 | ≦0.045 | ≦0.03 | 8.00-10.50 | 18.0-20.0 | – |
TP304 X5CrNi18-9 1.4301 | ≦0.08 | ≦1.00 | ≦2.00 | ≦0.045 | ≦0.03 | 8.00-11.00 | 18.0-20.0 | – |
316 X5CrNiMo17-12 1.4401 | ≦0.08 | ≦1.00 | ≦2.00 | ≦0.045 | ≦0.03 | 8.00-14.00 | 16.0-18.0 | Mo 2.00-3.00 |
301 X5CrNi17-7 1.4319 | ≦0.15 | ≦1.00 | ≦2.00 | ≦0.045 | ≦0.03 | 6.00-8.00 | 16.0-18.0 | – |
303 X10CrNiS18-9 1.4305 | ≦0.15 | ≦1.00 | ≦2.00 | ≦0.20 | ≧0.15 | 8.00-10.00 | 17.0-19.0 | * |
430 X6Cr17 1.4016 | ≦0.12 | ≦0.75 | ≦1.00 | ≦0.040 | ≦0.030 | – | 16.0-18.0 | – |
SCS13 G-X6CrNiMo18-10 1.4308 | ≦0.08 | ≦2.00 | ≦2.00 | ≦0.040 | ≦0.040 | 8.00-11.00 | 18.0-21.0 | – |
* Mo can be contained up to 0.60%
Besides below table of dimensions, we offer other dimensions and shapes. We often find special surface finish for the size such as thickness 4.00mm BA finish or Round billet of difficult to find stainless.
Category | Strip | Coil | Bar | Wire |
---|---|---|---|---|
Description | Cold Roll | Hot Roll & Cold Roll | Round, Flat, Hexagon | Round, Flat, Deformed |
Thickness (T) | 0.02~1.30mm | 0.25~1.50mm | 2.0~500.0mm | 0.0025~30.0mm |
Tolerance on T | ±10% of T~ | ±0.012mm~ | TBA | TBA |
Width (W) | 8.0~500.0mm | 300mm~500mm | – | – |
Tolerance on W | ±0.04mm~ | ±0.04mm~ | ±0.20mm~ | – |
Finish | Bright,Semi Bright, Dull | BA, 2D, No.1, No.4, 2B, hairline, emboss | Bright, Non Bright | Bright, Semi Bright, Dull |
Below table is for your to refer the appearance of each finish. We would like to remind you kindly that even the same finish, depending on steel mill, Sometimes the colors are different. We recommend you to double check the surface finish for only one side or double sided as well as avoid mixing different steel mills for your product if the surface finish is important.
Finish | Image | Description | Application |
---|---|---|---|
No.1 | ![]() | After hot rolling, annealed and pickled Silvery-white and non-shiny | Non surface gloss parts |
No.2D | ![]() | After cold rolling, annealed and pickled Gray low shine | General components Construction Materials |
No.4 | ![]() | Grinding with belt No. P150-P180 Shine, fine-grained | Automotive parts Food equipment Kitchenware |
No.2B | ![]() | Tension leveled on No.4 (Light cold rolling with mirror surface rolls) Smoother and slightly shinier than No.2D finish | General components Construction Materials |
BA | ![]() | After cold rolling, bright annealed (non-oxidation annealed) Shiny surface finish | Automotive parts Home appliances Kitchenware |
Hairline | ![]() | Polishing with P150 to P240 abrasive grain belt Long, continuous polishing grain | Construction Materials Machinery components |
Emboss | ![]() | Rolled by special rolls with etched or mechanically engraved patterns Uneven relief pattern | Construction Materials Decorative components |
304’s quality differs when the steel has significant stress such as changing shapes drastically and welding heavily, being exposed to the severe environment. The difference by steel mills come from steel mill’s quality management for minimizing contaminants and making uniform metallurgical structure. Some customers come to us appointing steel grade and steel mills together. Others have told us that some steel mills’ 304 cracks when they weld.
Besides metallurgical structures, there are issues such as corrosion (mentioned in details here), process precision (steel material must be in the defined tolerance range), and unexpected deformations (dents or wavy coils etc.) or appearance issues. We listen to your needs carefully to satisfy your QCD (Quality Cost Delivery) expectations.
As a professional steel vendor, Enseve would recommend 304 for any application where excellent corrosion resistance, weldability, and formability is required.
If you have any specific questions about 304 or similar stainless steels, please do not hesitate to contact us. We are always happy to help you customers find the best steel for your needs. We also often find steel materials of difficult-to-obtain grades and dimensions (reference examples). If you have any problems, we would be happy to discuss your problems with you.