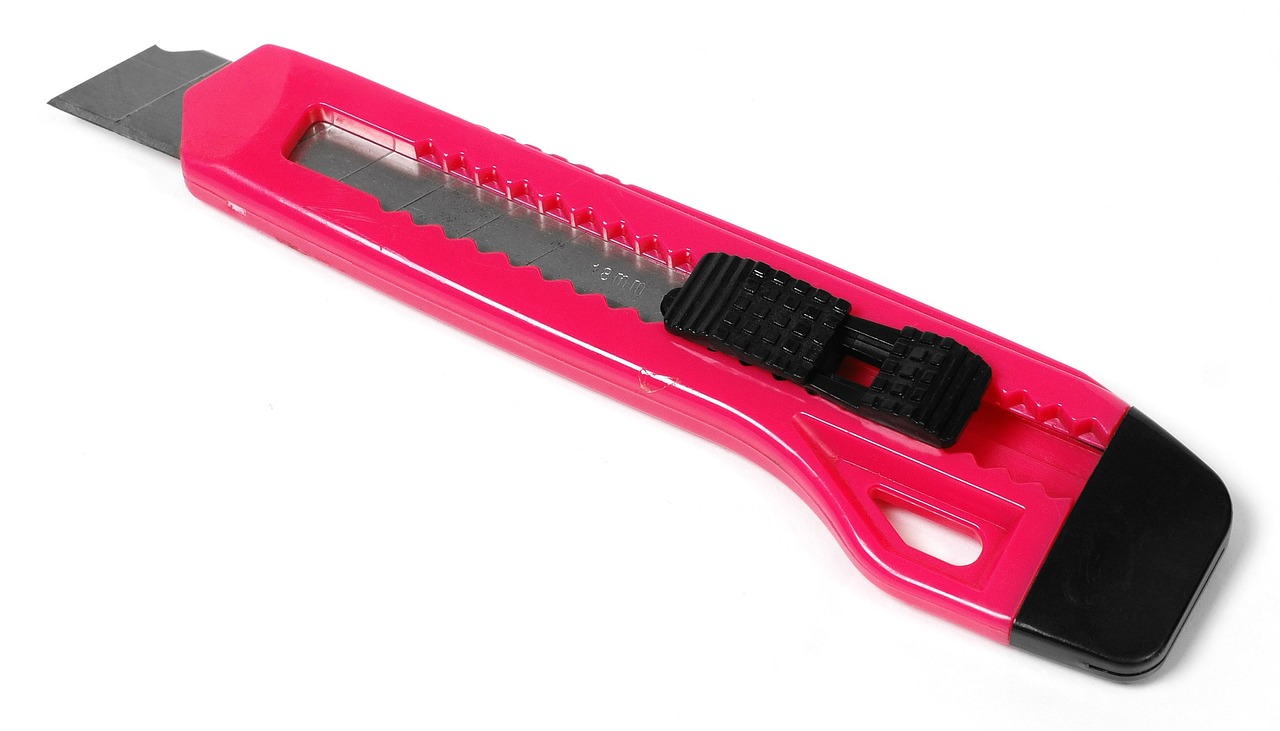
Carbon Tool Steels or high carbon steels are a kind of special steels (An introduction of special steels in general can be found here) and known for its high hardness, wear resistance, and elasticity. They are the most popular choice among cold-rolled special steel strips. In Japan, they are called SK series as Japanese abbreviation of “S (Steel)” and “K (Kougu = Tool)”. Outside Japan, this type of steels are also called “High Carbon Steel” or simply “Tool Steel”. In this page, we introduce the general properties of Carbon Tool Steels, Chemical Compositions by steel grades, dimensions and shapes available, and quality essence that we care about.
Carbon Tool Steels are typically heat treated to achieve its desired properties (hardness, wear resistance, elasticity). The heat treatment process involves heating the steel to a high temperature and then quenching it in water, oil, or special sub-zero environment to rapidly cool it. This process hardens the steel but also makes it more brittle. To reduce the brittleness (= increase toughness), the steel is then tempered by heating it to a lower temperature for a longer period of time.
Carbon Tool Steels are a high-quality steel that is well-suited for a wide range of demanding applications. It is important to choose the right grade of SK steel for the specific application, taking into account the required hardness, wear resistance, and toughness. Based on SK, there are variations of SK such as SKS (higher wear and impact resistance for cutting tools) , SKD (high hardness in high temperature environment for Dice or Molds), and SKT (resistant to thermal shock from heating and cooling for forging dies and die blocks).
We would like to point out kindly that Carbon Tool Steels have the weakness against the heat (Carbon Tool Steels are tempered or lose hardness in the temperature above 392℉ or 200℃). If you wish to maintain hardness above 392℉ or 200℃, usually SKH (High Speed Steel) is recommended. SKH series maintain hardness from 392℉ or 200℃ to 1112℉ or 600℃.
Carbon Tool Steels have a wide range of applications, including blades, cutting tools, springs, and other tools that require high performance.
SK series steel is graded according to its carbon content, with SK140 having the highest carbon content and SK65 having the lowest carbon content. The higher the carbon content, the harder and more wear-resistant the steel is, but also more brittle (image close to the glass). We would like to remark kindly that the hardness of the Carbon Tool steels increases mildly by the carbon content, while the wear and impact resistance varies according to the carbon content.
Below table demonstrates comparison of chemical compositions among similar steel grades from SK65(SK7) to SK140(SK1) with equivalent steel grades in the world. Chemical compositions are based on SK series basis, the equivalent steel grades are categorized according to the carbon content with slightly different chemical compositions other than carbons. The hardness (HRC) after quenching and tempering has also been added as a reference value.
Steel Grade | C | Si | Mn | P | S | Cr | Ni | HRC* |
---|---|---|---|---|---|---|---|---|
SK65 (SK7) W1-7 1065 060A67 060A72 C70W2 1.1620 C70E2U TC70 | 0.60~0.70 | 0.10~0.35 | 0.10~0.50 | ≦0.030 | ≦0.030 | ≦0.30 | ≦0.25 | ≧56 |
SK75 (SK6) 1075 060A81 C85W 1.1830 X75 TC80 | 0.70~0.80 | 0.10~0.35 | 0.10~0.50 | ≦0.030 | ≦0.030 | ≦0.30 | ≦0.25 | ≧57 |
SK85 (SK5) W1-8 1085 060A78 060A81 C80W1 C80E2U TC80 | 0.80~0.90 | 0.10~0.35 | 0.10~0.50 | ≦0.030 | ≦0.030 | ≦0.30 | ≦0.25 | ≧59 |
SK95 (SK4) W1-9 1095 C105E2U TC105 | 0.90~1.00 | 0.10~0.35 | 0.10~0.50 | ≦0.030 | ≦0.030 | ≦0.30 | ≦0.25 | ≧61 |
SK105 (SK3) W1-10 1,407 105CR2 1.3501 C105E2U TC105 | 1.00~1.10 | 0.10~0.35 | 0.10~0.50 | ≦0.030 | ≦0.030 | ≦0.30 | ≦0.25 | ≧61 |
SK120 (SK2) W1-11 1025 1,407 125CR2 1.2002 C120E3U TC120 | 1.15~1.25 | 0.10~0.35 | 0.10~0.50 | ≦0.030 | ≦0.030 | ≦0.30 | ≦0.25 | ≧62 |
SK140 (SK1) C130W2 C140E3U TC140 | 1.30-1.50 | 0.10~0.35 | 0.10~0.50 | ≦0.030 | ≦0.030 | ≦0.30 | ≦0.25 | ≧63 |
HRC* is reference Hardness after quenching and tempering
Besides below table of shapes, we can offer other shapes and processed form.
Category | Strip | Coil | Bar | Wire |
---|---|---|---|---|
Description | Cold Roll | Hot Roll & Cold Roll | Round, Flat, Hexagon | Round, Flat, Deformed |
Thickness (T) | 0.02~1.30mm | 0.25~1.50mm | 2.0~500.0mm | 0.0025~30.0mm |
Tolerance on T | ±10% of T~ | ±0.012mm~ | TBA | TBA |
Width (W) | 8.0~500.0mm | 300mm~500mm | – | – |
Tolerance on W | ±0.04mm~ | ±0.04mm~ | ±0.20mm~ | – |
Finish | Bright,Semi Bright, Dull | BA, 2D, No.4 | Bright, Non Bright | Bright, Semi Bright, Dull |
To improve machinability, sharpness and durability for applications (such as cutting tools), the carbides of tool steels must be small and spheroidised (round) as uniformly as possible. Spheroidisation annealing must be carried out before quenching and tempering process. The key to the successful Spheroidisation annealing operation is sufficient heating time and gentle cooling afterwards.
Besides metallurgical structures, there are issues such as corrosion (high carbon steels are easy to rust), process precision (steel material must be in the defined tolerance range), and unexpected deformations (dents or wavy coils etc.) or appearance issues.
We listen to your needs carefully to satisfy QCD (Quality Cost Delivery) expectations.
As a professional steel vendor, Enseve would recommend SK series steel for any application where high hardness, wear resistance, or elasticity is required. It is also a relatively affordable steel, making it a good value for the money.
If you have any specific questions about SK series steel or need help choosing the right grade for your application, please do not hesitate to contact us. We are always happy to help you customers find the best steel for your needs. We also often find steel materials of difficult-to-obtain grades and dimensions, including SK materials (reference examples). If you have any problems, we would be happy to discuss your problems with you.