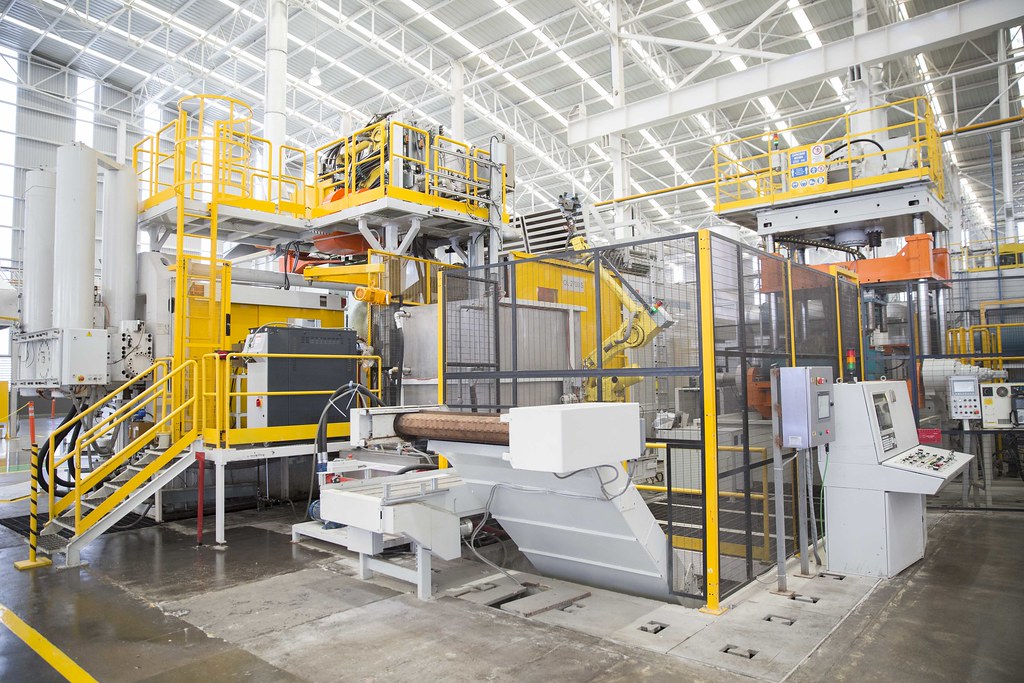
Aluminum die casting is a manufacturing method in which parts can be produced by melting aluminum at a high temperature, pressing it into a mold (shot), and cooling it. Die casting has excellent precision, appearance, and productivity, so it is widely used from mobile phone cases to automobile parts.
The time required for one shot (hereinafter referred to as cycle time) is generally about 30 to 60 seconds, and shortening the cycle time by 1 second directly leads to productivity improvement, saving a total of tens of hours a year. In addition to reducing the cost per shot, there are also secondary effects such as cutting overtime hours, improving labor shortage, reducing carbon emission gases, and improving the site and performing QC activities in the spare time, and further improving productivity and quality. Therefore, each die cast company is working to shorten the cycle time.
In general, die cast companies devise a mechanism to cool the mold and speed up each operation. In this article, I would like to introduce a cycle time shortening method that has been “common in Europe and the United States”. For some reason, the traditional method remains popular in East Asia.
Going straight to the point, “Switch the plunger tip to an inexpensive copper alloy.” In this article, I would like to talk about 1) What is a Plunger Tip?, 2) The Current Situation about the Plunger Tip in East Asian Market, 3) Proposal from Enserve, and 4) Future Prospects.
In the first place, the plunger tip is a tip part that extrudes the molten aluminum inside an aluminum die casting machine. The performance required for the plunger tip is as follows.
- Durability against high temperature and high pressure
- Sealing property for nest measures
- Stability against heat conduction and dimensional changes (thermal expansion) for cycle time stability
While the plunger tip can a standard part for each diameter, some die casting machine users (hereinafter referred to as die casters) customize their plunger tips. In addition, the plunger tip is subject to considerable high temperature and impact, so it wears out during use and is an expendable item that needs to be replaced. The plunger tip is an important expendable supply for die casting machines that controls quality and productivity.
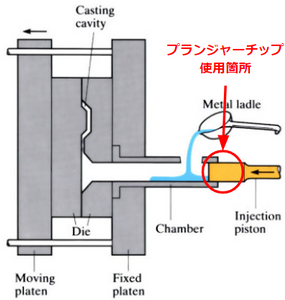
In East Asia (particularly Japan), Steel (alloy steel such as SKD61) is the mainstream for plunger chips, and Thermal spraying, regeneration, and combinations of steel and copper alloys are also available. Die casters often use plunger tips until operators detect abnormalities about plunger tips (strange noise, irregular molten aluminum flow, etc). Then the operators replace the old plunger chips to the new ones and discard the old ones.
The commercial distribution is roughly as follows. Trading companies in “()” may or may not be present depending on die casters’ need. Intestingly, unlike printer ink (an expendable item for printing which manufactures strictly accept only genuine inks and cancel warranty for compatible inks), a drawing of the plunger chip is attached when die casters purchase a die casting machine. Refering to that drawing, die casters procure plunger chips through their own commercial distribution.
- Die cast machine manufacturer -(trading company)- Plunger chip manufacturer
- Large Daicaster -(large maintenance company)- Plunger chip manufacturer
- Mid-size Daicaster- (Med-size maintenance company)- Plunger chip manufacturer
Characteristically, many diecasters rely on a handful of plunger chip makers. Since the plunger tip is a consumable item, steel has been popular material due to the cost. Some non-steel tips exist, but their use may be limited. On the other hand, plunger tips in Europe and the United States have been switched from steel to copper alloy. The reason is high productivity, and die casting machine manufacturers also use copper alloy plunger chips as standard, so as various automobile manufacturers. “We know the existence of copper alloy plunger tips in Japan, but they are not common due to the cost.” said the Japan Foundry Engineering Society (reference). The reason why copper alloys increase productivity is that aluminum solidifies faster and cycle time is shortened. Specifically, from the injection of molten aluminum as shown in the figure below to the opening of the mold, when solidifying aluminum, copper alloy has good heat dissipation and solidification is faster (the seconds shown are samples). Copper alloys also have the advantages of longer life than iron, less frequent equipment outages due to replacement, and less annual usage than iron.
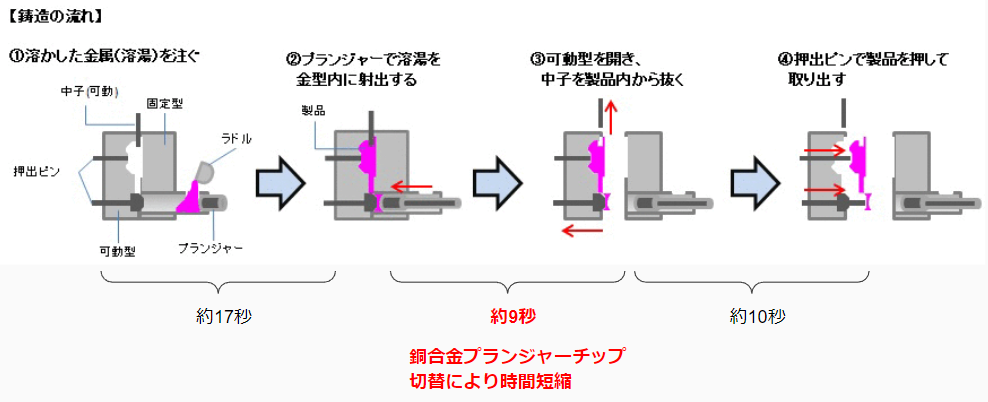
We also made a trial calculation and found that every time the cycle time was shortened by 1 second, it was possible to save about 4,000 USD per die-casting machine per year, or 94 hours in terms of time (including equipment, labor, consumables costs, based on 2 shifts). If die casters have multiple lines, the savings will be greater (if you fill out the application form, we will distribute an Excel sheet to estimate the savings benefits for free).
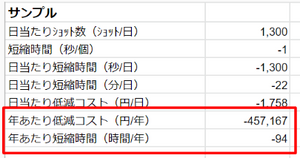
Copper alloy plunger tips are highly productive but expensive. Thus, our proposal is to import inexpensive copper alloy plunger tips from overseas manufacturers with abundant experience and know-hows. The advantages of our proposal are cost reduction (reduction of equipment cost, labor cost, indirect cost per shot), reduction of overtime hours for workers, creation of surplus time (time allocation for improving productivity and quality), and disadvantage of higher cost for plunger chips. The annual cost for copper plungers may increase. If the advantages outweigh the disadvantages, I think there is room for consideration of evaluation and switching. In addition, since it is imported from overseas, some people may be concerned about quality, cost competitiveness, and impact on current plunger chip makers, so I will explain our views on each.

- Quality When it comes to imports, many Japanese people would have quality concerns. In fact, since the plunger tip is exposed to high temperature and high pressure, it cannot be used stably unless the material properties are excellent. Since our manufacturer has abundant delivery records to die casting equipment manufacturers and automobile manufacturers in Europe, it produces multiple types of copper alloys exclusively for plunger chips. Based on our records and know-how, there is a possibility that it will be accepted in Japan in terms of quality.
- Cost Competitiveness Unlike plunger makers in East Asia, our manufacturer is cost-competitive in that they carry out integrated production from materials to machining. Regarding the effects of the exchange rate and inflation, the appreciation of the USD has taken place over the last decade. Inflation in the country of manufacture is also present, but on a USD basis, the USD is appreciating in a way that offsets inflation, and as a result, the impact on prices at the time of purchase is not that great.
- Impact on Current Plunger Chip Makers We will also positively consider selling only the material (bar) to plunger chip makers. Since the proposed manufacturer only produces plunger chips with a diameter of 60 mm or more, we are willing to collaborate with plunger chip manufacturers according to circumstances such as diameter, small-quantity production, risk of damage during transportation, and difficulty in changing commercial distribution.
Adopting copper alloy plunger tips gives benefit for all related parties.
- Die cast machine manufacturers : Improvement of product added value and product differentiation
- Die casters : Manufacturing cost reduction
- Chip makers : Addition of new value-added products and product differentiation
We are also looking for partners such as die casting machine manufacturers, die casters who can jointly verify the advantages, and plunger chip manufacturers who can design and process customized products according to die caster needs. Please feel free to contact us for collaboration or the form to estimate the benefit of copper alloy pluger tips as writing “I would like an Excel sheet for studying copper alloy plunger tips”.
We believe that it is valuable to increase productivity of die casting not only in Japan but also throughout Asia. We would be grateful if you could collaborate with us.
Thank you.