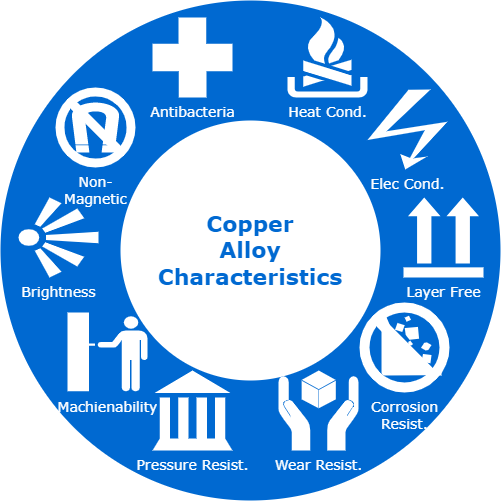
Copper is said to be the first metal used by humans who began to use tools. The discovery of copper, a metal that is easy to smelt and has excellent workability and durability, brought many benefits to mankind as hunting became more efficient, agricultural production increased, and resources were exploited, resulting in accelerated population growth and concentration of wealth, leading to the emergence of urban civilization. Later, the mainstream metalware such as vessels and weapons in ancient times shifted from copper to iron, but copper’s importance in the development of modern industry also increased over time due to the enhanced characteristics of copper with other chemicals. This article introduces 10 properties and advantages of copper alloy in comparison with steel for your reference. First of all, this article describes “copper alloy“, not “pure copper (copper with purity of 99.90% or higher is called pure copper)”. The copper alloy enhances physical and mechanical properties by adding some chemicals to pure copper. Copper alloy own below characteristics for specific needs.
There are 10 distinct propeties of copper alloy which many applications are created. We decribe one by one with some application examples.
# | 10 Properties & Advantages of Copper Alloy |
---|---|
1 | Heat Conductivity |
2 | Electronic Conductivity |
3 | Layer Free |
4 | Corrosion Resistance |
5 | Wear Resistance |
6 | Pressure Resistance |
7 | Machinability |
8 | Brightness |
9 | Non-Magnetic |
10 | Anti-Bacteria |
Some copper alloys conduct heat about 4~7 times faster than steel does. In fact, copper’s heat conductivity is higher than aluminium. Some fancy restaurants use copper pans due to high heat conductivity. The heat is transferred quickly and evenly, resulting in less uneven baking and a mellower, gentler flavor. If you need to heat up or cooldown quickly, copper alloy might be a good choice. Application example : Plunger tips for aluminium diecast and Cooking tools
The most electrically conductive metals (lowest electrical resistance) are, in order, silver > copper > gold > aluminum. However, copper is almost as conductive as silver (94% of silver at room temperature) and is much less expensive than silver, which is a precious metal. So copper is almost always used for electric wires and other applications that require high electric conductivity. Some copper alloys conduct electricity about 5 times faster than steel does. Application example : Resistant welding material, Electrical cable
For aluminium die casting, steel forms an Al-Fe compound layer at the point of contact with aluminum, causing seizure (overheating due to frictional heat and alteration of material surface). This compound layer may adhere to the aluminum, resulting in an expansion of the wall thickness, which may cause cracks or other defects. Meanwhile, some copper alloys do not create an Al-Cu compound layer and prevents seizure. Application example : Plunger tips for aluminium diecast
Steels corrode, while copper alloys corrode very slowly. Copper can protect the metal inside by creating a type of rust on its surface called a passive film. Although corrosion cannot be completely stopped, it can be controlled to a fairly low level, just as many bronze (a kind of copper alloy) coins can be cleaned as soon as it comes into contact with vinegar. For this reason, bronze is used for statues and for coins (in Japan all coins except for one yen). This is also the reason why bronze vessels and armor from long ago (Bronze Age) are excavated in good condition. For example, ancient copper products are sometimes excavated in their original form because copper is a rust-resistant metal. In addition, aging / precipitation treatment (*) forms a dense oxide film on the surface of copper alloy, which acts as a protective film and provides excellent oxidation resistance at high temperatures. Application example : Ship’s screws and Roofs. *Age hardening treatment is a heat treatment for copper alloys that disperses fine precipitate particles of intermetallic compounds to increase strength. For example, the addition of 2% beryllium increases strength by 600% over pure copper (the proposed material contains 0.4-0.7% beryllium).
The better the wear resistance, the higher the life of the metal. Generally, the harder the metal, the better the wear resistance. However, in comparison between copper alloy and steel, some copper alloys are superior at wear resistance due to adhesion of metals. Wear takes place for four reasons. There are some Copper Alloys that are superior to steels. Application example : Plunger tips for aluminium diecast
<4 reasons of wear>
- Adhesion of friction surface metals to each other
- Adhesion resistance to oxide film and other contaminants
- Surface roughness
- Material strength (tensile strength, hardness)
Considering these reasons, ideal metal for wear resistance would be the following. For example, in plunger tips for aluminum die casting, a chemical reaction between aluminum and iron forms a film (Al-Fe compound layer), which easily causes wear, while aluminum and copper alloys do not form a film and are not susceptible to wear.
- Combination of less cohesive metals (copper alloys contain many additives and avoid friction thus copper alloys cause less wear)
- Film (incl. lubricats) that prevents oxide film or other contaminants (copper alloys cause less corrosion thus copper alloys cause less wear)
- Smooth surface or surface with a large number of contact points (Surface smoothness depends on the machining accuracy)
- Hardness and strength (In general tool steel is harder than copper alloy thus tool steel causes less wear for this point)
Some copper alloys such as bronze are said to be Pressure resistant. Pressure resistance can be broken down by hardness and tensile strength (the higher these indeces, the more difficult to change shape by high pressure). In general, tool steel such has better pressure resistance property than copper alloys. Still one of our copper alloy has better pressure resistance property than SKD61. We make a sample comparison among SKD61 (representative Tool Steel), C63000 (Bronze Copper Alloy), and our original copper alloy.
SKD61 : Hardness HB420, tensile strength 1250N/mm2
C63000 : Hardness HB160, tensile strength 620N/mm2
Our original copper alloy : Hardness HB420, Tensile strength 1750N/mm2
Application example : Die material
Generally, Copper has excellent cutting ability, but it is highly tenacious and prone to burring. Since the material is sensitive to heat and softens at temperatures above 200°C, manufacturers of copper alloys have the following know-hows.
- Fast cutting speed
- Usage of sharp tools with a large rake angle
- Use oil-based coolant suitable for cutting copper (water-based coolant will discolor copper alloys)
- In the case of beryllium copper, dust control measures are taken (beryllium is harmful to the human body)
Some Copper alloys such as brass are the only one other than gold with a golden luster. Applications : funiture components
Some Copper alloys are non-magnetic. For example, belirium copper is non-magnetic while bronze is slight magnetic. Applications : Gears
Copper is often used on doorknobs, handrails, and other areas that are touched by many people and prone to the growth of bacteria. It has been scientifically proven that the trace metallic action of copper ions, which has the property of killing bacteria, is effective against bacteria. There are other metals with antimicrobial properties, but copper is not too expensive like gold or silver, nor is it poisonous like lead. Recently, copper door openers and other copper products have been distributed to prevent coronavirus contact infection. Application example : furniture components
Enserve has a strong network with copper alloy manufacturer that routinely produce special, rare copper alloys. Please feel free to contact us if you have been refused by other copper alloy companies or if you have any problems with copper alloys.