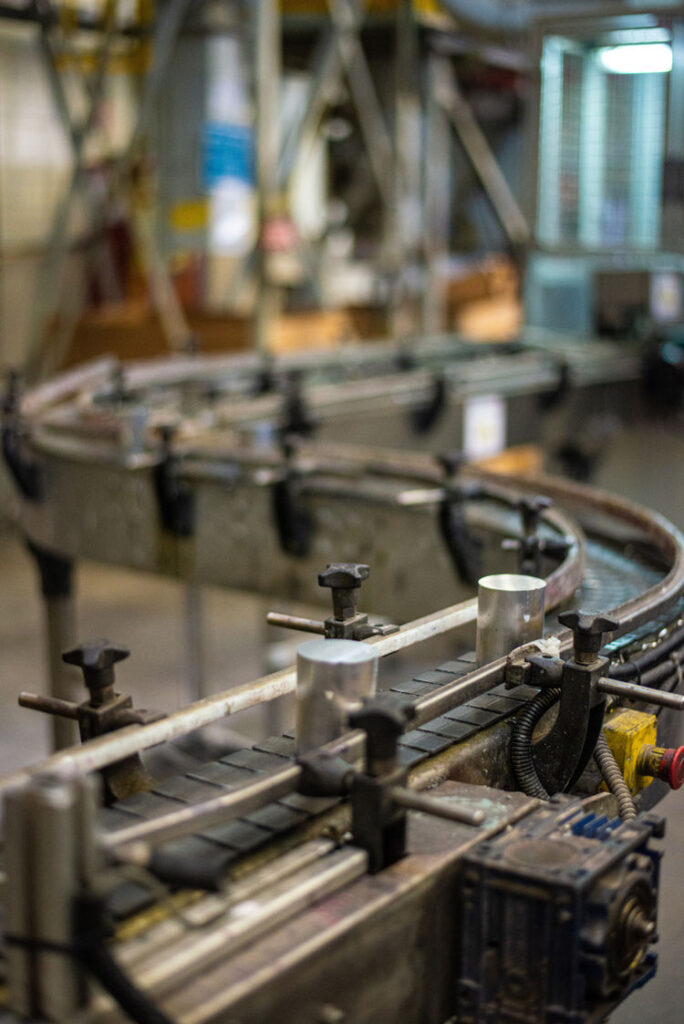
For small-medium manufacturing businesses, it is often difficult to calculate the cost of manufacturing accurately for many reasons. One of the reason is often “simply they do not know how to calculate”. As a result, quotation prices vary each time and unfortunately they cannot explain for cost increases. To solve these problems, we would like to share some basic concepts of breaking down the cost into unit costs. This article would be useful for those who work at small-medium manufacturing business.
Breaking the cost is straight forward. First, you can segregate cost of good into “material cost”, “processing cost (including inspection)”, and “shipping cost (including packing)”. Then, you can break down each category into “unit cost” x “units for production”.
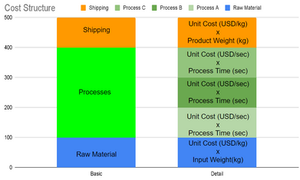
We would like to demonstrate a simple example would be an aluminium die cast. To make it simple, we assume there are only die casting process and inspection proces. No machining. No surface treatment such as Black Alumite. Cost structrure would be only “raw material”, “die casting”, and “inspection”.
- Raw Material Cost Say, you need to inject 0.2kg/pc of aluminium and aluminium ingot price is 2USD/kg. You can calculate the cost of raw material as 0.4USD/pc (0.2kg/pc x 2USD/kg = 0.4USD/pc). For simplification purpose, we ignore yield rate for now.
- Die Casting Process As you download a sample from here, it is simple to follow by filling in yellow cells. There are further breakdowns such as total working minutes/year, Equipment cost/minute, Euipment operating cost/minute, Labor cost/minute, and mold cost.
- Total working minutes/year you can fill in yellow cells below to calculate total working minutes for an aluminium die cast machine. Operational Availability ratio is a bit tricky so we explain for you. The Operational Availability Rate (the ratio of the time the machine is actually running, excluding the time it is stopped for mold changes and various adjustments). Assuming the machine stops for about 1.5 hours per shift, it is set to 81.25% (8 hours – 1.5 hours = 6.5 hours/8 hours = 81.25%). The result of this example is that a die cast machine works (excluding any downtime) for 202800 minutes per year.

- Equipment cost/minute You can fill in yellow cells below to calculate equipment cost per minute. You may need to ask your accounting team for support. In this example, it costs 0.28USD/min for the equipment itself.

- Euipment operating cost/minute You can fill in yellow cells below to calculate equipment operating cost per minute. You can consult your accounting team, take some record of energy use and so on. In this example, it costs 0.17USD/min for equipment operating cost.

- Labor cost/minute Labor costs are a bit tricky to explain. Labor costs are broken down into man-rate and number of units. The man-rate is the cost per worker, including salary, social security, training, etc. For example, if a worker is paid 2,770USD per month, including overtime, the man-rate is around 5,540USD, or 0.46 yen per minute. Next is the number of units, which is the number of people operating the equipment per unit. For example, if one person is looking after three machines, the number of units is 0.33 (1÷3=0.33) persons/unit. Then, you can fill in the manufacturing overhead costs. This is the manufacturing overhead counts for transportation, repairs, inspections, etc. It would be easier to understand if you consider how many people are in these indirect departments compared to those in direct manufacturing. For example, if there are 10 people in direct manufacturing and 2~3 people in indirect manufacturing, it would be 25%.

- Mold cost Lastly, you can calculate the mold costs. In this example, the mold life is expected to be 30,000 shots, while the mold cost is 26,923USD. The mold cost per shot is 26,923USD/30,000shots = 0.09USD/shot.

- Aluminium die casting process Total We asuume “process time” is 36seconds or 0.60min per shot (36 sec/pc ÷60sec/min=0.60min/pc). The unit cost (All the cost per minute to operate) for die cast machine is 0.62USD/min. Thus equipment labor costs for this example is 0.37USD/pc (0.60 min/pc x 0.62USD/min = 0.37USD/pc). Also, it costs 0.09USD/pc for a mold resulting in the total cost per aluminium die casting process + inspection is 0.46USD/pc.
- Total Cost of this example Raw material is 0.40USD/pc and process cost is 0.46USD/pc. Thus the total cost of this example is 0.86USD/pc (0.40 + 0.46 =0.86).
There are several parameters that affect greatly the unit cost.
- Amotization Years It can be the same as the legal durable years. Actual machines last longer and so you can set actual durable years. (The fewer the yars, the higher the cost)
- Operating Availability Rate It is often difficult to measure first hand. You may use simple sensors to measure. The critical reasons to decrease this rate can be “long mold changing time” “Frequent small down times” “accumulation of small wating time” etc.
- Number of Units “Person/Machine This number relies basically on automation level and frequent small down time.
- Machine Cost It is critical to purchase machine cost at reasonable price. Often small companies purchase high price machines with more features and end up not using the additinal features.
You can contact us for free a tool to calculate the cost of a component/products. We plan to keep updating other examples for your reference. Also, if you have trouble in using the tool, we would be happy to help you also.