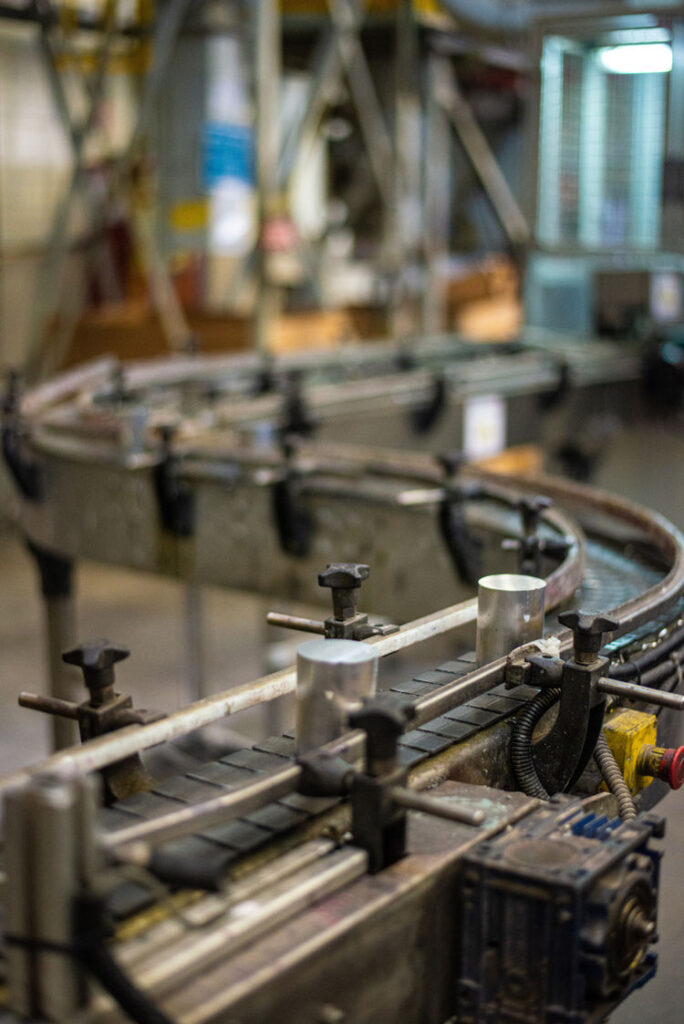
中小製造業にとっては、様々な理由から、製造原価を正確に計算することは難しかったりします。理由のひとつとして、「単純に計算の仕方がわからない」ケースもございます。その結果、見積もり価格が毎回大きく変動してしまい、原価上昇がなぜおきてしまったのか説明ができないことがあります。そこで、今回は「原価を単価に分解する」という基本的な考え方をお伝えしたいと思います。中小企業にお勤めの方は、ぜひ参考にして頂けますと幸いです。
原価を分解していくのはシンプルです。まず、商品の原価を「材料費」「加工費(検品含む)」「輸送費(梱包含む)」に分別することができます。そして、それぞれのカテゴリーで 単価×生産用単位に分解すれ流れになります。
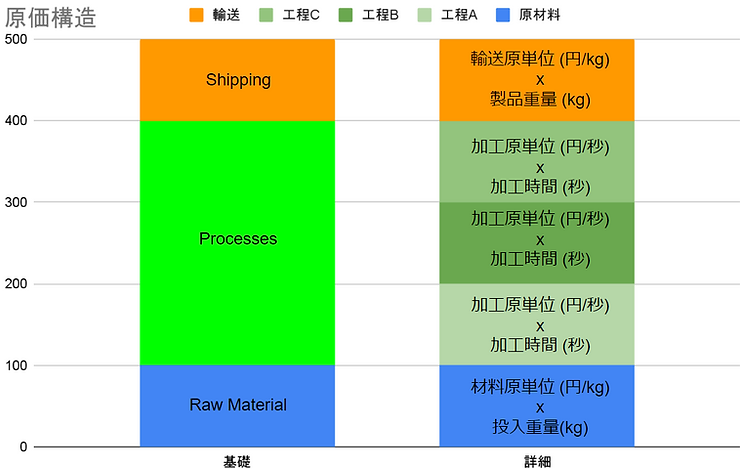
例として、アルミダイカストについて説明したいと思います。ここでは簡易的にダイカスト工程と検査工程のみとします。機械加工や黒アルマイトのような表面処理もない前提です。コスト構造は、「原材料」「ダイカスト」「検査」のみとなります。
- 原材料 例えば、アルミダイカストで0.2kg/個で投入する必要があり、アルミニウムインゴットの価格が200円/kgであるとします。原材料のコストは40円/個と計算できます(0.2kg/個 x 200円/kg = 40円/個)。簡略化のため、歩留まりは率は無視します。
- ダイカスト工程 こちらからサンプルをダウンロードしていただき、黄色いセルに記入することで簡単に見ることができます。さらに、総作業時間/年、設備費/分、設備運転費/分、人件費/分、金型費などの内訳があります。記入方法は以下の通りです。
- 総作業時間/年 アルミダイキャストマシンの総稼働時間を計算するには、下の黄色いセルのように記入頂きます。可動率については、少し難しいので、説明します。可動率(金型交換や各種調整のために停止している時間を除いた、実際に機械が動いている時間の割合)です。機械が1シフトあたり約1.5時間停止すると仮定すると、81.25%(8時間-1.5時間=6.5時間/8時間=81.25%)に設定されます。この例の結果、ダイカストマシンは年間202800分稼働(ダウンタイムを除く)することになります。

- 設備コスト/分 下の黄色いセルに入力すると、1分あたりの設備コストを計算することができます。もしかしたら経理の方の協力が必要かもしれません。この例では、設備自体に35.98円/分のコストがかかっています。

- 設備稼働コスト/分 下の黄色いセルを埋めることで、1分あたりの設備稼働コストを計算します。経理担当者に相談したり、電気・ガスの使用量の調べられるとよいかと思います。こちらの例では、設備稼働コストは22.68円/分となります。
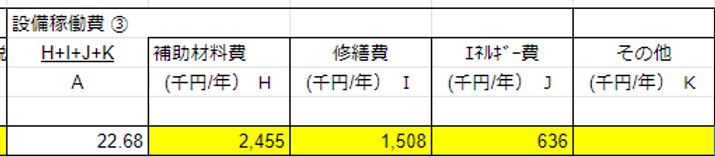
- 人件費/分 人件費とは、給与、社会保険、研修などを含めた労働者一人当たりのコストのことです。労務費はマンレートと持ち台数に分解されます。マンレートとは作業者の方の給与・社会保障・研修などをいれた1人あたりの費用を記入致します。一般的には給与の2倍の金額が社員1人あたりに発生すると言われており、例えば、残業代なども入れ月36万円程の給与が発生するようであれば、2倍の72万円、1分あたりだと60円程がマンレートとなります。続いて持ち台数ですが、1台あたり何人が設備の運用をしているかになります。例えば3台を1人で見ているようであれば、0.33(1÷3=0.33)人/台となります。最後に製造補助部門日になります。これは運搬、修繕、検査等の製造間接費となります。これはこれらの間接部門の方々が直接製造の方々と比べてどれくらいの人数かで考えて頂けると分かりやすいかと思います。例えば、直接製造が10人、間接製造の方々が2~3人くらいならば25%となります。

- 型費/ショット 最後に、1ショットあたりの型費を計算します。こちら例では、寿命は30,000ショットと予想して、型費は3,500,000円となります。1ショットあたりの費用は、3,500,000円/30,000回数= 11.67円/ショットとなります。
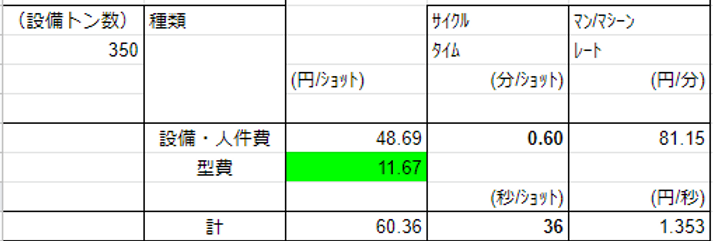
- アルミダイカスト工程 合計 加工時間は、1ショットあたり36秒、0.60分(36秒/個÷60秒/分=0.60分/個)と仮定します。ダイカストマシンの単価(1分あたりの稼動コスト)は81.15円/分です。従って、この例の設備人件費は48.69円/個(0.60分/個 x 81.15円/分 = 48.69円/個)です。また、型費が 11.67円/個 かかるので、アルミニウム ダイカスト 工程+ 検査あたりの総費用は 60.36円/個となります。
- この例における総費用 原材料は40円/個、加工・検査費は60.36円/個です。したがって、この例の総原価は100.36円/個(40 + 60.36 =100.36)です。
この考え方をすると、単価(時間あたりコストなど)×生産用単位(加工時間など)に分けて原価の内訳を考える事ができます。その中で、単価に影響を与えるいくつかの重要なパラメーターをご紹介したいと思います。
- 償却年数 法定耐用年数と同じにできます。ただ、実際設備はもっと長持ちするので、実耐久年数で設定することができます(年数が少ないほどコストが高くなります)。
- 可動率 実際に測定するのは難しい場合が多いですが、簡単なセンサーで測定することができます。”鋳型交換時間が長い””稼働停止が頻繁に発生する””小さな待機時間の積み重ね”などは、稼働率を下げる大きな理由となります。
- 台数(人/機械) この数値は、基本的に自動化レベルと頻繁に発生する小さな稼働停止時間に依存します。
- 設備費 設備費そのものを安く抑えることも重要です。中小企業では、より多くの機能を備えた高価な機械を購入し、結局はその追加機能を使用しないまま終わってしまうことがあります。こういった事を避けるため事前に何が本当に必要なのか、全て内製する必要があるのかを検討頂く事が大切となります。
部品・製品のコストを計算するツールは、ご連絡いただければから無料でダウンロードできます。今後、他の事例も随時更新していく予定ですので、ご参考にして頂けますと幸いです。また、ツールの使い方でお困りのことがありましたら、お気軽にご相談ください。